New report: Preparing for the future of battery manufacturing
The latest Workforce Foresighting report, produced in collaboration with the WMG, University of Warwick and sponsored by the UK Battery Industrialisation Centre (UKBIC), provides a comprehensive analysis of the skills and capabilities required for the assembly of lithium-ion battery modules and packs for transport. This study, conducted by the Workforce Foresighting Hub, an Innovate UK initiative, highlights the urgent need for workforce transformation to support the UK’s transition to battery electric vehicles (BEVs).
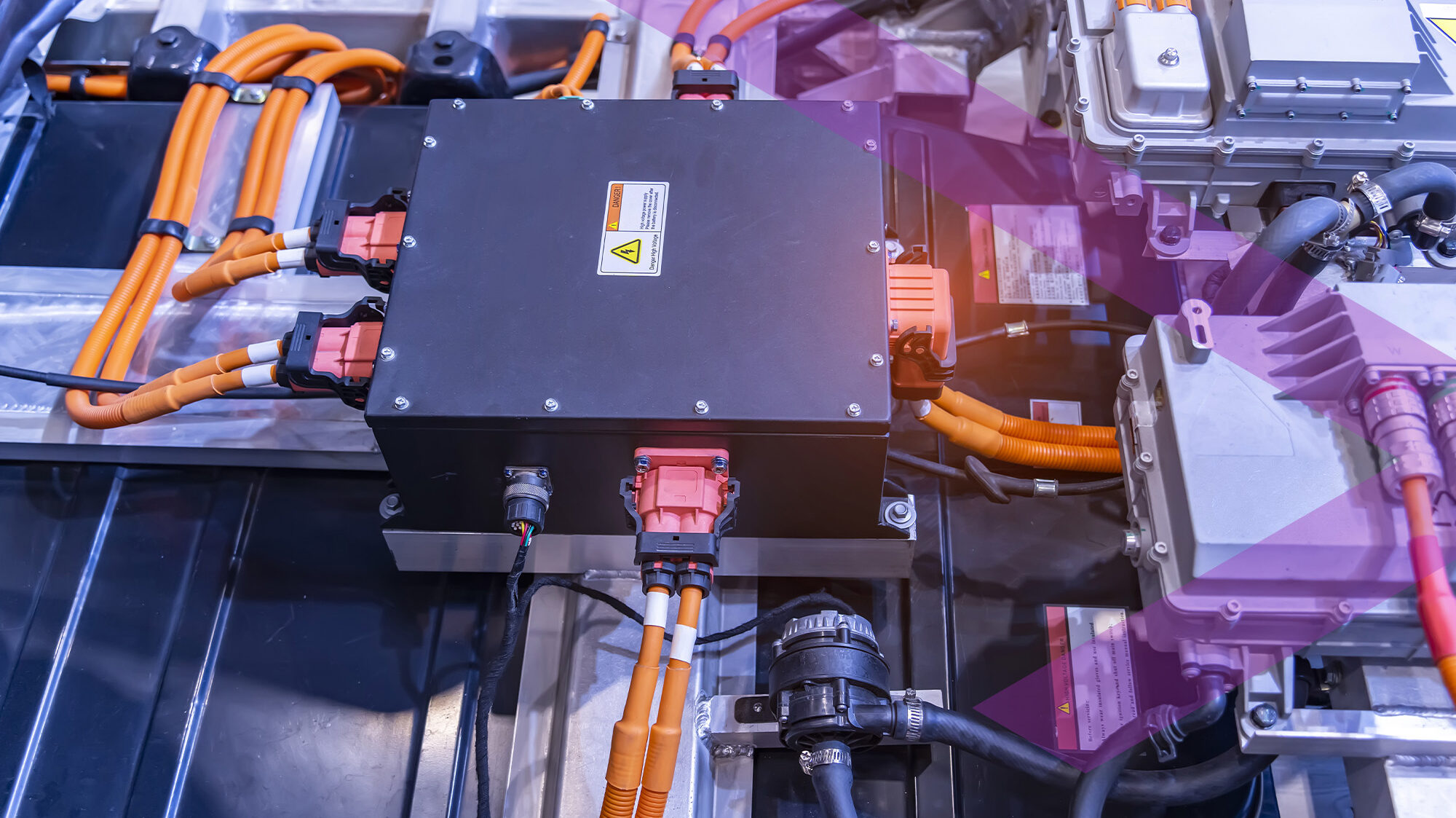
Workforce Foresighting: A systemic approach
Workforce foresighting is a strategic method of planning ahead to anticipate future skills and capability needs associated with new technologies and government transformation targets. It involves identifying and understanding the skills required for tomorrow’s jobs, ensuring that education and training systems are prepared so that the workforce is ready to adopt new technologies and support future industrial growth.
Key findings of the report
The report sets out the findings of the workforce foresighting study and suggests the next recommended actions required by various stakeholders to ensure a workforce is created that is prepared to effectively implement these new technologies in the sector:
-
Skills anticipation
The report emphasises the importance of foresighting to identify future skills required for new technologies and government transformation targets. This proactive approach ensures that education and training systems are aligned with industry needs.
-
Workforce reskilling
The shift to BEVs demands significant reskilling of the existing workforce. Manufacturers must reconfigure assembly operations and invest in retooling production lines to accommodate BEV manufacturing at scale.
-
Sector-wide impact
The transition affects not only the automotive sector but also other transport modes, including rail, aerospace, marine, and micromobility solutions. Tens of thousands of workers will need retraining for module and pack assembly.
-
Educational programmes
The report calls for the development of new apprenticeship standards, longer-term education programmes, and rapid reskill initiatives. Professional bodies play a crucial role in certifying skills and promoting excellence through professional registers and safety standards.
The UK’s transition to BEVs
The UK’s transition to battery electric vehicles (BEVs) presents a critical shift for vehicle manufacturers, requiring a fundamental transformation in production lines, workforce capabilities, and supply chain strategies. To remain competitive and achieve climate targets, manufacturers must rapidly reconfigure assembly operations, particularly in battery module and pack integration, while navigating significant workforce reskilling demands. This shift will have a profound impact on human resources, requiring new expertise in electrification technologies, as well as on production infrastructure, necessitating investment in retooling existing lines to accommodate BEV manufacturing at scale.
Next steps and recommendations
The report underscores the need to act not just in the future but also in the shorter term to enable the skills transition. Competencies are evolving, and this report demonstrates this, but the challenge for some time will be the scale and speed of the shift. Therefore, rapid industry, government, and provider buy-in will be required. This report provides employers with guidance on what they need to look for in provision, supports providers to identify what provision is needed and what capabilities they need to acquire to meet industry needs, and enables the government to better understand the needs of both parties to better support them with informed policy. Addressing these skills gaps is crucial to ensuring the UK remains competitive, sustainable, and capable of supporting its net-zero ambitions.
Summary of next steps:
- Leverage the Electrification Skills Network (ESN) as the primary forum for action
- Validate future occupational profiles (FOPs)
- Identify a sector champion for workforce development
- Develop an action plan for immediate and mid-term needs
- Evaluate opportunities for further workforce foresighting studies
Conclusion
The time for action is now, requiring coordinated efforts across industry, government, professional bodies, and education providers to build a workforce fit for the future. Failure to act decisively will have long-term consequences for the UK’s industrial competitiveness, workforce sustainability, and ability to meet net-zero targets. If these skills gaps are not addressed, UK-based manufacturers risk falling behind global competitors, and supply chain resilience will be compromised. Urgent collaboration is needed to ensure that the workforce transition keeps pace with technological advancements—securing jobs, investment, and leadership in module and pack assembly.
Related programmes
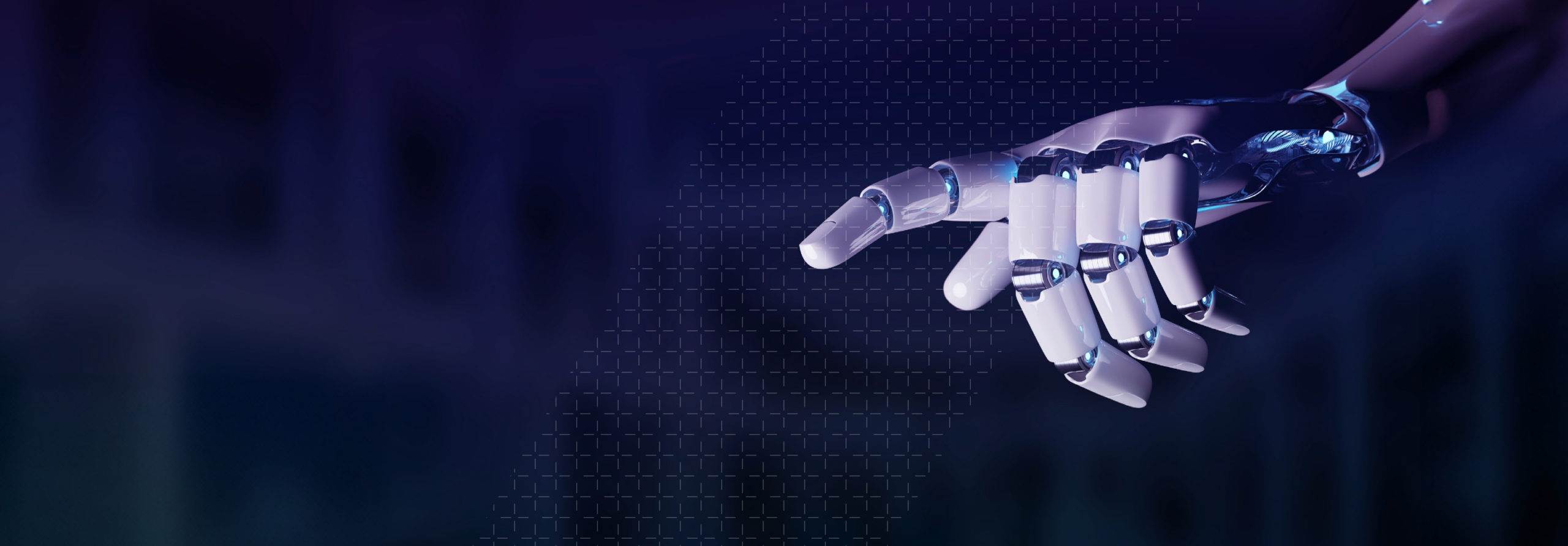
Workforce Foresighting
How do we build a skilled workforce for tomorrow’s industries? The Workforce Foresighting Hub has developed a structured process, aligned with national policy, to help deliver a workforce to exploit innovative technologies in the UK. We’re supporting industry, policymakers and educators to adapt to continuing change.
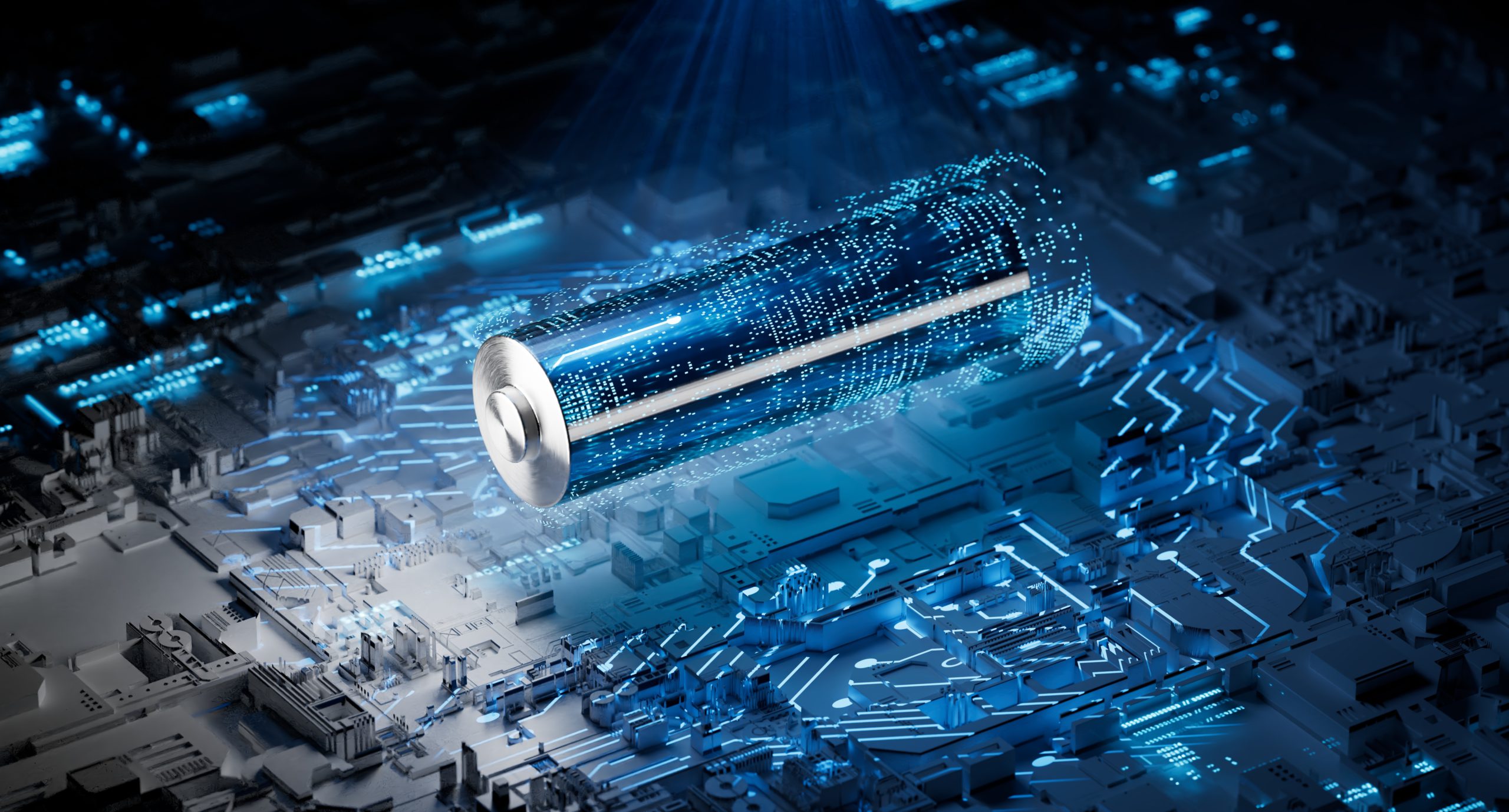
Cross-Sector Battery Systems Innovation Network
The Cross-Sector Battery Systems Innovation Network, co-founded by Innovate UK and the Faraday Battery Challenge, is a cross-sectoral and collaborative community of technology developers and end-users.