Future-proofing UK metalworking SMEs: integrating robotics and workforce development
The Manufacturing Technology Centre (MTC), in collaboration with the Workforce Foresighting Hub, an Innovate UK initiative, has released a new report, The adoption of robot automation in metalworking SMEs. This report presents the findings from the Workforce Foresighting cycle, focusing on developing an integrated process for adopting robot automation in metalworking SMEs. The study aims to identify the steps needed to start to prepare the workforce and enable robotics automation for future industrial growth.
Importance of the metalworking sector
The UK metalworking sector is vital to the economy, contributing significantly to GDP and supporting industries like construction and automotive. Automation in this sector can enhance productivity, reduce costs, and improve quality, addressing challenges such as labour shortages and high energy costs. National growth plans, including the Steel Strategy and Invest 2035, aim to modernise the industry, promote sustainability, and create jobs.
This cycle was commissioned to identify the new capabilities the metalworking SME sector needs to gain momentum in automation adoption. While this is the primary focus, no sector can undergo a transformation without working with its closest supply chain partners who will also need to adapt to realise this ambition. Examples of enabling supply chain partners include robotic manufacturers, system integrators, and finance organisations, often large multinational companies. The analysis looks at all four partners and the capabilities each needs to improve or gain to enable automation adoption in the metalworking SME sector. This means that while the study identifies specific areas of focus for SMEs, it also considers the wider sector change needed to help SMEs adopt more robotics and automation. The two are intrinsically linked and need to be looked at together to understand the full implications of the changes needed.
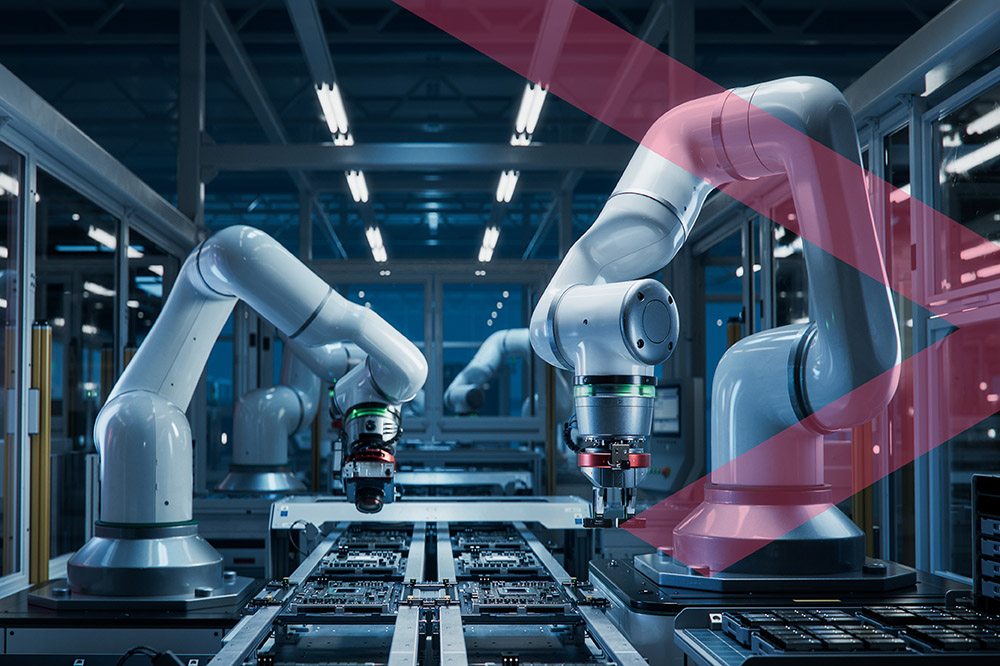
Growth in robotics adoption
The UK has seen significant growth in robotics adoption across various sectors, including metalworking. In 2023, the UK installed a record 3,830 industrial robots, a 51% increase from the previous year. Despite this growth, the UK’s overall use of robotics remains relatively low compared to other Western European countries.
Challenges in the metalworking sector
The metalworking sector faces several challenges impacting its efficiency and profitability:
- High Energy Costs: Automation can optimise energy usage, reducing overall consumption.
- Labour Shortages and Skills Gap: Automation can take over repetitive tasks, allowing the workforce to focus on more complex activities.
- Supply Chain Disruptions: Automated systems can improve supply chain management through real-time data and analytics.
- Quality Consistency: Automation ensures high precision and consistency in manufacturing processes.
- Cost Management: Automation can reduce labour costs and material waste, leading to significant cost savings.
- Workplace Safety: Automation can handle hazardous tasks, reducing the risk of workplace accidents.
Importance of workforce development
While integrating automation is important, technological adaptation without the right skills and workforce is ineffective. A sustainable approach needs to focus on both technology and workforce development to reach its full potential. The World Economic Forum highlights that 54% of all employees will require significant reskilling and upskilling by 2025.
Findings and insights
The analysis of over 175 future state capabilities needed by the metalworking SME industry for robotic and automation integration has revealed significant insights:
- Larger organisations typically equip their employees with these capabilities through on-the-job training, an approach not feasible for SMEs due to limited resources.
- Alternative solutions include integrating relevant content into degree or apprenticeship courses and supporting SMEs in upskilling their employees.
- While future state capabilities are the foundation of the research, further analysis has been conducted. One key analysis is the Future Occupational Profiles (FOPs), which combine capabilities to generate future job roles. FOPs can effectively identify gaps that job roles may face due to technological changes.
Next steps
To meet the needs of SME end users, it is important to address gaps in provision related to procurement with appropriate and accessible solutions. Developing short courses for upskilling existing staff is a current priority, with longer-term integration of these courses into Level 3 and Level 4 apprenticeships. A working group, led by Automate UK, should be convened with interested parties from the educational sector to develop and deliver the appropriate training programs. This group would disseminate the report’s outcomes, lead detailed analysis, and implement an action plan.
The anticipated outcomes include a range of reskilling and upskilling courses, modular changes to existing training programs, and major revisions of existing provisions. Regular dialogue between educators, awarding bodies, and employers is essential to ensure the output meets the sector’s needs. The working group should also review findings with stakeholders regularly, adapting Future Occupational Profiles (FOPs) as needed to ensure a good fit as robot automation technology develops and new roles emerge.
In conclusion, clear gaps in skills provision have been identified, proving to be barriers to robot automation adoption. Immediate and coordinated efforts by educators, employers, and other stakeholders are essential to address these skills gaps and ensure the sector’s growth and sustainability.
Related programme
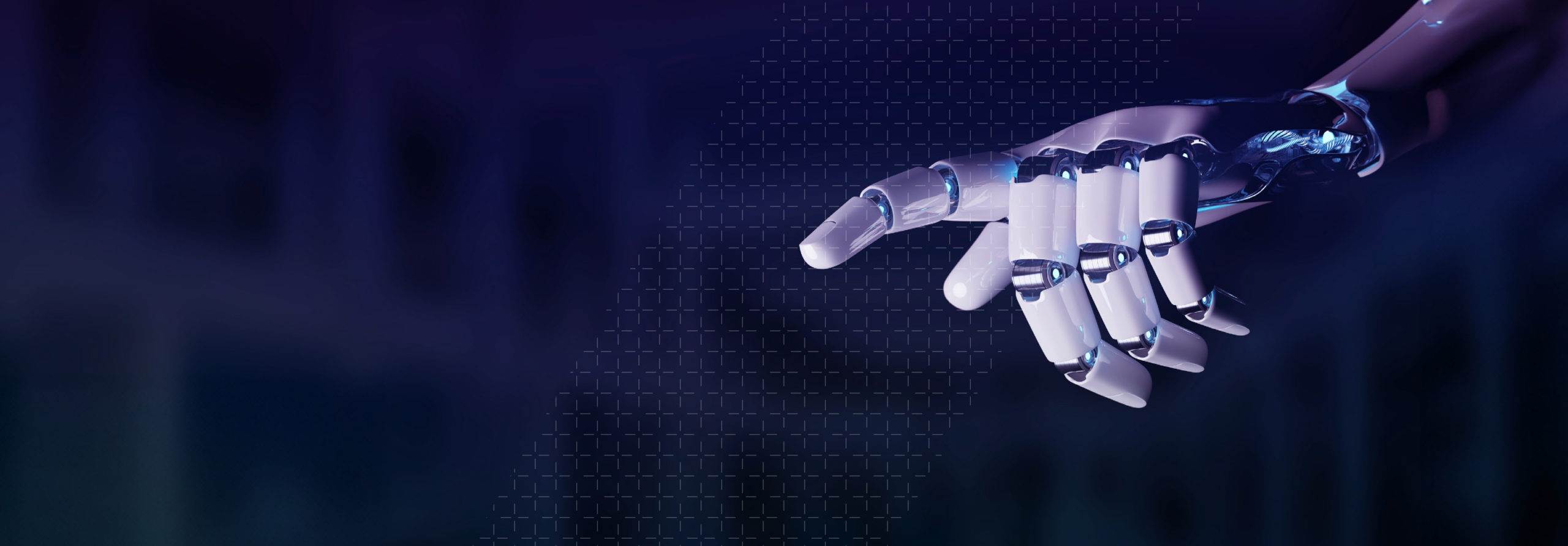
Workforce Foresighting
How do we build a skilled workforce for tomorrow’s industries? The Workforce Foresighting Hub has developed a structured process, aligned with national policy, to help deliver a workforce to exploit innovative technologies in the UK. We’re supporting industry, policymakers and educators to adapt to continuing change.