Mevocrete: the journey of a collaborative research and development project leading to a deployed industrial-scale plant and private investment. The collaborative approach led by innovative SME Material Evolution, has been creating circular approaches for the manufacture of innovative concrete.
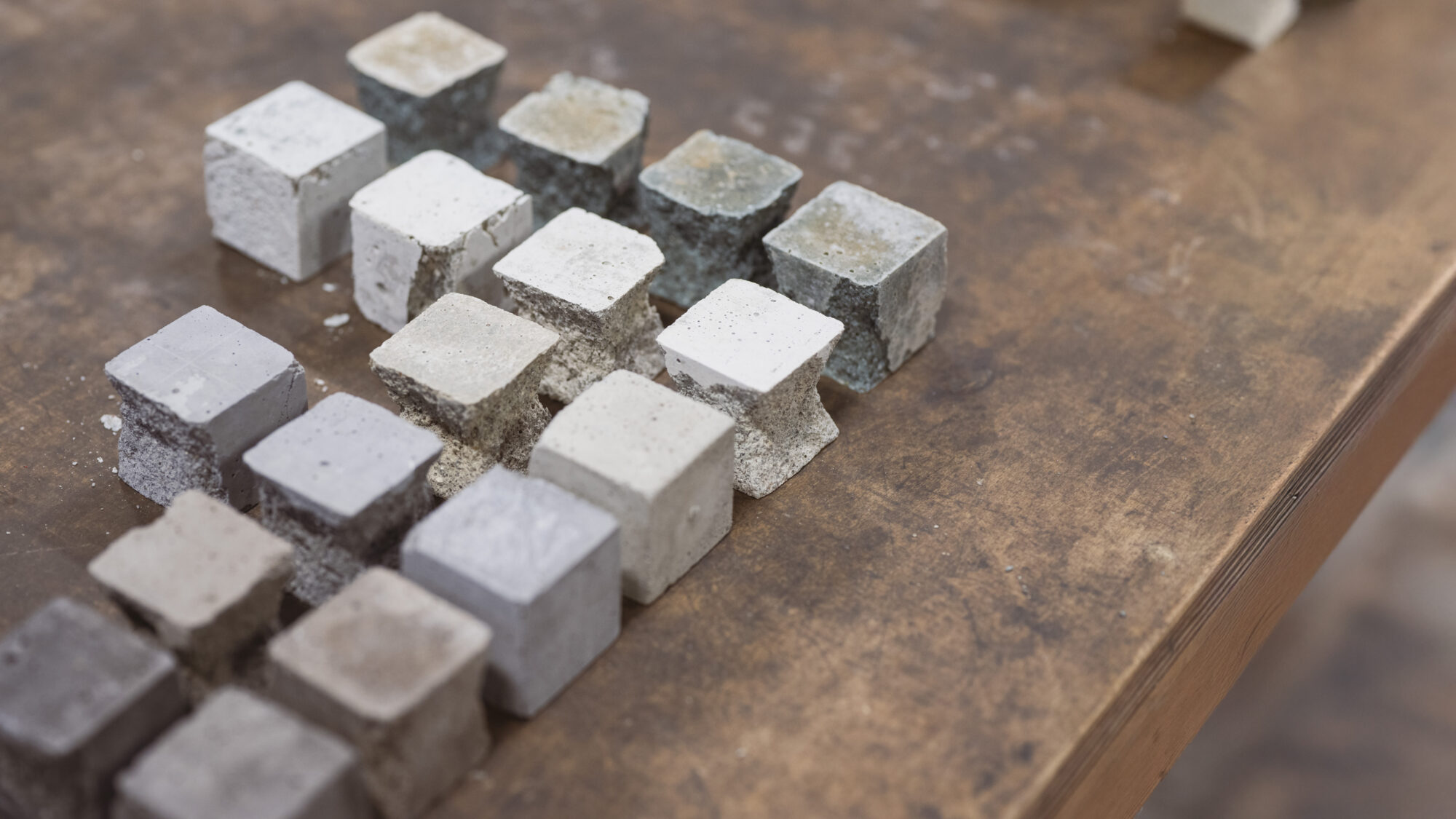
Collaborative approach
Material Evolution, a start-up materials engineering company embarked on leading a cross-sector collaboration with Celsa Steel which was supported by the UKRI Transforming Foundation Industries (TFI) challenge, delivered by Innovate UK, Engineering and Physical Sciences Research Council and Economic and Social Research Council. The outcomes from this project led to formation of the Mevocrete consortium to scale-up the innovation for a TFI demonstrator funded project, where Material Evolution and Celsa Steel were joined by Enursan, Materials Processing Institute, LKAB, Nanomox, Teesside University and ZTL Contracting/Retaining UK/Geocast (Applebridge Group).
The Mevocrete Project shows the power of cross-industry partnerships in delivering innovative and sustainable solutions. By breaking industry barriers, we can foster innovation, establish circular practices, reduce emissions, and create new supply chains. Thanks to the funding from Innovate UK, we have achieved significant results in both R&D product development and market delivery.
– Sam Clark – COO and Co-founder, Material Evolution
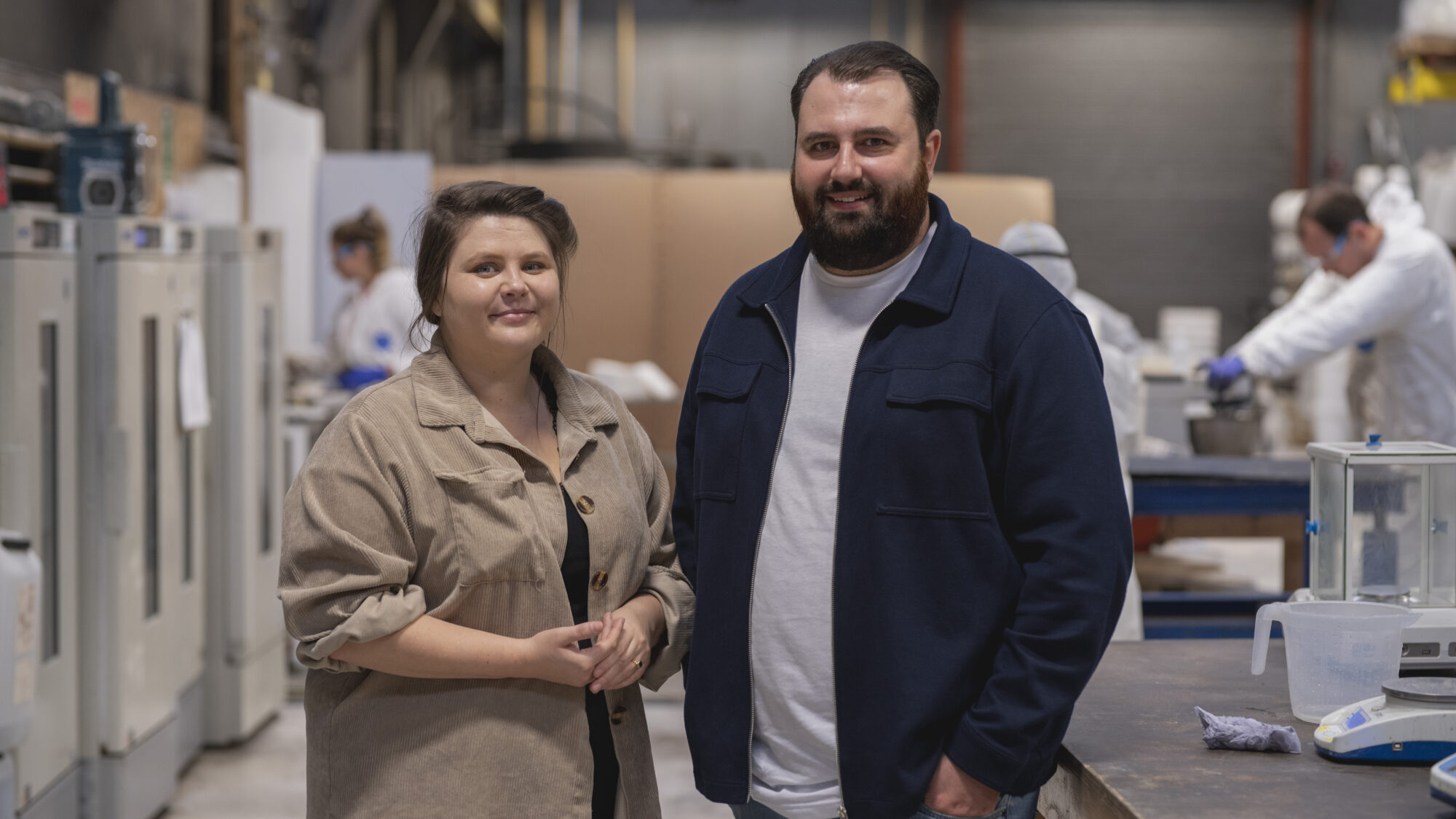
Background
The steel industry produces Ground Granulated Blast furnace Slag (GGBS) which can be reused as a cementitious material to create more durable and lower-carbon concrete. With the phasing out of blast furnaces and the increased use of more energy efficient Electric Arc Furnaces (EAF), the availability of GGBS is reducing. Though the EAFs themselves produce a black and white slag waste, it is not currently suitable to replace GGBS as a cementitious material.
Opportunity
The situation gives rise to an opportunity to develop a methodology and demonstrate that black slag waste (which makes up the majority of the slag volume) from Electric Arc Furnaces can replace GGBS as a cementitious material for the continued production of lower-carbon concrete. Valorisation of a by-product material, that has little to no value and is often landfilled allowed for the transformation of the black slag to make a cement additive (SCM) that excels in terms of economics and sustainability. A successful collaborative research and development project then paved the way for a further opportunity to scale-up the technology for a demonstrator.
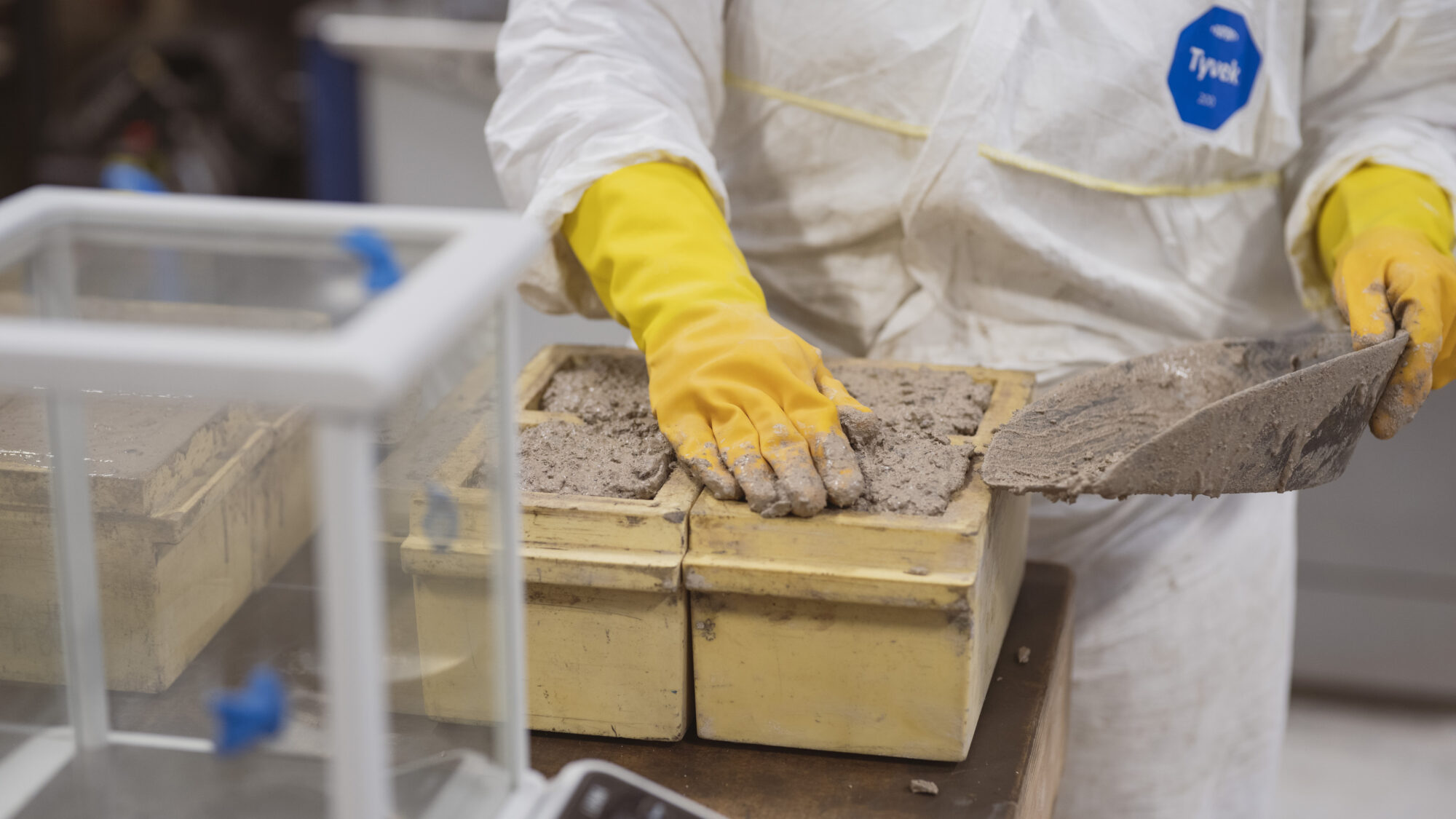
Innovative solution
Material Evolution’s platform technology uses a proprietary process called ‘alkali fusion’, plus geopolymer chemistry and advanced algorithms to create bespoke mixes from industrial by-products like EAF slags. The Material Evolution team analysed several waste streams including black and white slags and their patented technology used complex machine-learning modelling to develop bespoke formulations for producing different types of cement and concrete. Test pours validated the modelling for structural, durability, workability and curing behaviour tests. This was followed by successful production trial in Material Evolution facilities.
During the demonstrator project the team focused on expanding the scope of the previous work to include the entire supply-chain to develop a carbon-negative concrete at industrial scale independently evaluated by Teesside University. The project required further development of the teams understanding as it looked for novel, rationalised production process which were readily scalable/deployable. Material Evolution again made use of its technology to create and test the materials at batch/industrial scale leading to large scale demonstration pours, scalable geopolymer demonstrated at scale and hot slag trials.
These projects have led to the creation of a new, first-of-a-kind cement production plant in Wrexham. The facility produced its first batch in October 2024 and is operating on an industrial scale with the capacity to produce 120,000 tonnes of the MevoCem product. This demonstrates how collaborative projects can lead to new industry being rooted in the UK.
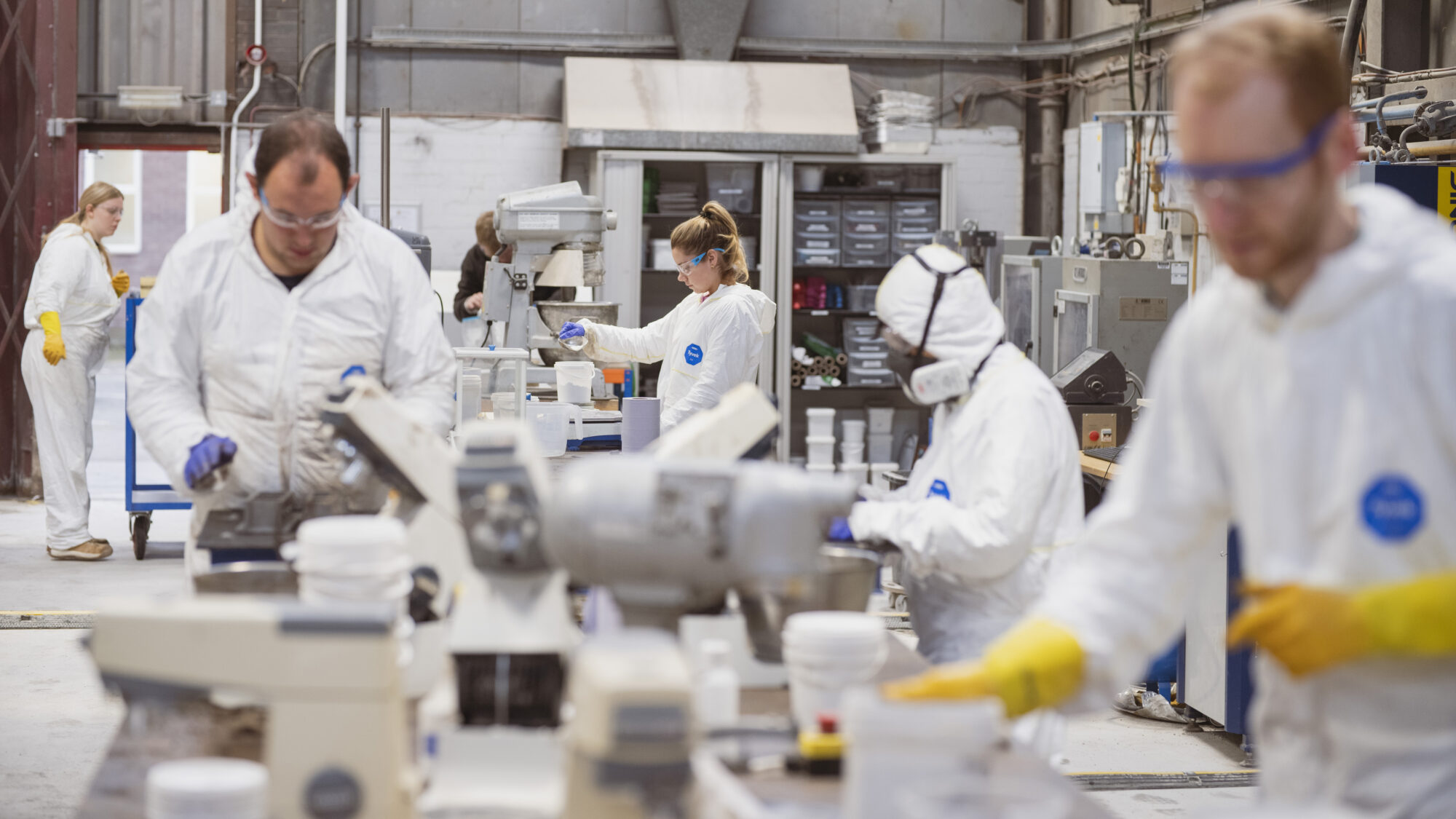
Impact
- A successful collaborative research and development project enabled Material Evolution along with Celsa Steel to form the larger consortium for the TFI demonstrator project
- Material Evolution have raised private equity to bring their products to market and the technology developed has been used to launch Material Evolution’s first of a kind UK facility for the manufacture of ultra-low carbon cement
- Both projects successfully led to the demonstration of Material Evolutions patented technology to use EAF by-products to manufacture a cement additive with environmental and economic benefits
- Material Evolution can design bespoke cement mixes using its machine learning algorithm.
- Celsa Steel were able to establish an outlet for its EAF slag material and its commercial value
- Nanomox Ltd were able to prove and scale-up their OIS® Process for producing new materials from their novel metals recovery technology
- LKAB were able to deploy the demonstrator system and derisk a new supply chain and the processing of an alternative feedstock
- ZTL Contracting / Retaining UK / Geocast were able to establish new green construction practices for brown-field construction projects
- Materials Processing Institute and Teesside University were able to increase know how and expertise
- The success of this project shows how collaborative research and development can support the advancement of innovation, the growth and future investment opportunities
Role of collaborators
Large Scale R&D project & Demonstrator Project:
- Material Evolution Ltd – A small materials engineering consultancy company with the innovative solution to creating sustainable cement
- Celsa Steel UK Ltd – A large UK steel recycling company manufacturing reinforcing steel bars for use in concrete, and provider of the projects waste by-product
For the demonstrator project Material Evolution Ltd and Celsa Steel UK were joined by:
- Materials Processing Institute – A research and innovation organisation developing advanced materials and commercialising technologies with expertise in steel slags and materials characterisation
- LKAB – A large Swedish supplier of iron ore, minerals and specialist products deploying the demonstrator system at an industrial relevant scale
- Nanomox Ltd – Technology company developing sustainable advanced materials conducted a pre-production valorisation study, a chemical leachate isolation and provided input into the demonstrator system
- Teesside University – Provided testing capabilities and expertise in carbon sequestration and UKAS accredited testing
- ZTL Contracting / Retaining UK / Geocast (Applebridge Group) – Large engineering group covering a range of construction disciplines provided soil stabilisation, pre-cast architectural and non-structural commercial trials
Find out more
Discover more about collaborative projects supported by UKRI’s Transforming Foundation Industries Challenge: