Navigating the design to manufacture journey: Design Processes and Principles
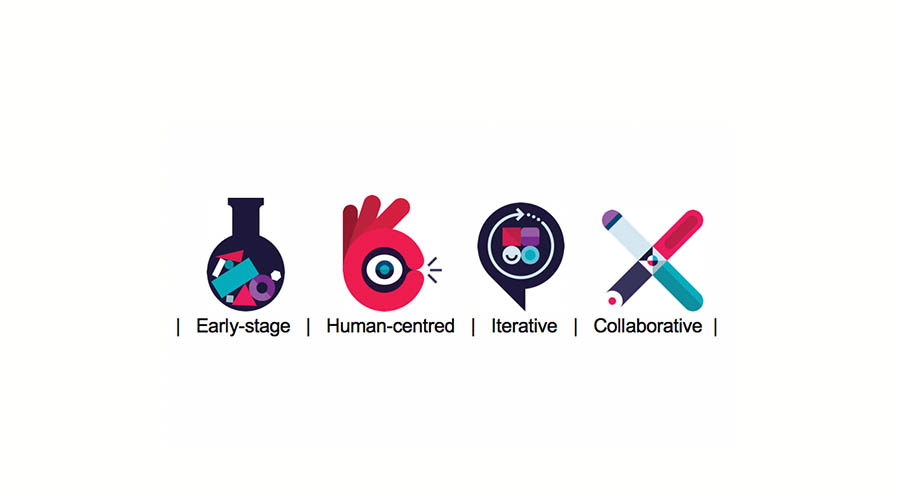
Design is the activity of de-risking an innovation. It involves a plethora of activities from understanding to idea generation, analysis and formalisation of idea.
We find that hardware innovators have a tendency to focus on the functionality of their design and have a predisposition to neglect the bigger picture. It’s often said that generating ideas is easy and we could argue that this is largely true – methods such as IDEO method cards can help with this process. The skill and craft of design comes in de-risking these ideas in order to make them a reality. In this blog Erica de Melo Carvalho, Innovation Caucus Intern and Abi Hird from our Manufacturing Team focus on ways and means of making that happen based on a recent online webinar session hosted as part of our Navigating the Design to Manufacture Journey series.
Consider design in the context of the wider innovation process
Design can be an unwieldy process. Having a process with some form of structure will act as a map. It will break up a project and enable you to understand where you are, where you are going and why. Only when you know where you’re meant to be, are you able to really see when you are lost. The Design Councils Double Diamond or Pugh’s Total Design Methodology are just two of many examples.
A guide that is commonly used in the development of innovative physical products is Technology Readiness Level (TRL) scale. Originally developed by NASA as a means of managing complexity and uncertainty around Innovation, other variations have been derived such as this one used by 4C design.
TRL’s are also accompanied by a Manufacturing Readiness Levels (MRLs) – originally developed by the Department of Defence, these provide a guide to the maturity of the manufacturing plan. Following these scales enables understanding of what did not work before moving on, providing a systematic approach.
One thing we have noticed is that innovators are predisposed to be overly optimistic about how far along the TRL scale they truly are. Whilst some of their innovation is advanced, often other questions are left unanswered. This article provides a holistic view of the process and the Innovation Canvas provides a toolset to help you think about all the factors you need to consider as you develop your innovation.
With hardware it is especially important to think holistically
Using a Design for ‘X’ approach you can start to focus and target different design elements throughout the design process, such Design for Manufacture, Design for Cost, Design for Test, Design for Procurement, Design for Assembly, Design for Logistics, Design for Security etc.
Utilise design and manufacturing standards and best practice to optimise your product. Use checklists to build confidence and to ensure you consider all requirements. Tools such as Computer Aided Design (CAD) can help. As you implement and review the design rules, check your CAD model to ensure that you have designed for manufacture. Our friends at Invent Design Build have developed a guide to some common product approvals.
Involve manufacturers in design as early as possible. Early design choices can impact manufacturability. A common mistake is to engage with manufacturers only when you want to move to production. Review the manufacturer’s capabilities, request Design for Manufacture (DfM) guidelines as well as their input as you design. Dragon Innovation has a great free-to-access Design for Manufacture resource.
Modelling and prototyping are powerful and essential
Prototypes are essentially a model used for the purpose of communicating your ideas. Although we tend to conceptualise them as physical models, they can be computer simulations, sketches, mathematical models or verbal summaries.
Prototypes allow feedback to be gained by checking assumptions, perhaps by gathering the opinions of users or other stakeholders or, by testing. They can also be used to communicate ideas or a vision with a view to getting buy-in or investment.
Low cost, low fidelity prototypes using readily available craft materials can quickly isolate and resolve problems. They can give potential customers a first “trial” of your product and aid in testing and trying to understand how a technical part of the product operates. You can use things like Lego, foam, paper, bits of string, plasticine etc. For example, Google Glass. Google trialled the process of projecting information into the user’s field of view using an LCD screen attached to a piece of coat hanger strapped to a pair of glasses to see whether people could tolerate having information in their field of view.
More expensive higher fidelity prototypes should be used only when essential. They are useful for exploring final performance characteristics and manufacturing routes. When developing high fidelity prototypes remember they are not the end goal! The end goal is to de-risk an idea enough to reach your end goal (scaling up, continuing to invest in the idea).
Navigating the Design to Manufacture Journey Series
We ran a series of weekly webinars – Navigating the Design to Manufacture Journey – during #lockdown, where we engaged with a number of industry experts exploring all aspects of systems thinking from funding and investment to scaling up manufacturing. If you managed to join us for some or all of these webinars, great. If not, you can catch up on recordings from the series here.