Learn how a Resource Efficiency for Materials and Manufacturing (REforMM) feasibility study enabled Weffan to investigate the optimisation of machinery, forge crucial UK partnerships, and develop a business case for 3D woven garments.
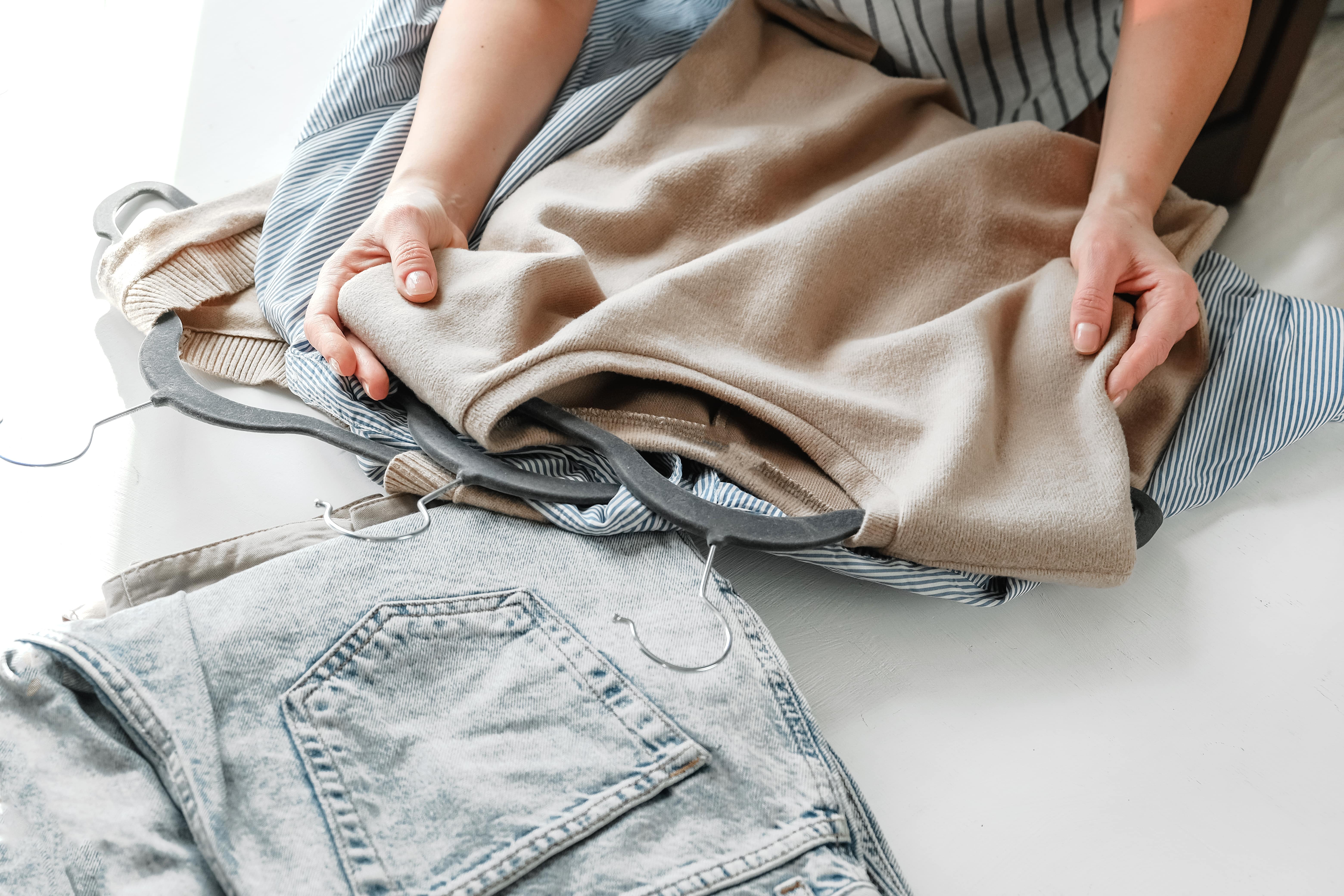
Weffan is revolutionising the fashion industry with a low-waste, localised whole-garment production system using 3D weaving technology.
Here, Graysha Audren, Founder and COO and her team share how an Innovate UK Resource efficiency for materials and manufacturing feasibility study enabled Weffan to investigate the optimisation of machinery, develop a business case for 3D woven garments, and forge crucial UK partnerships.
The feasibility study allowed us to test our concept of the technology, market, and commercial viability which could ultimately improve resource efficiency in fashion manufacturing.
Efficiency Challenges in Fashion Manufacturing
The UK fashion industry, which supports 1.3 million jobs and generates £23 billion a year in tax revenue, faces significant sustainability challenges. 15-20% of material is wasted on the manufacturing floor alone due to outdated methods. Globalisation has led to offshoring, diminishing UK manufacturing capabilities.
As a startup tackling this multifaceted problem, Weffan faced a daunting task.
We’re essentially redesigning how clothes are made. It requires a holistic approach to the entire supply chain, which is deeply complex and entrenched in out-dated, globalised practices.
Revolutionising Garment Manufacturing with 3D Weaving
Weffan’s innovative approach combines textile and garment manufacturing into a single step using existing Jacquard machines. To achieve their objectives, Weffan: Partnered with the University of Leeds’ 3D Weaving Innovation Centre to explore both immediate commercial goals and long-term technological solutions.
Engaged with industrial partners in the UK and EU to understand how their technology could integrate into existing supply chains.
Throughout the study, Weffan maintained a structured yet flexible approach. They set clear project goals and work packages, held regular progress meetings, and remained adaptable to new insights and challenges as they arose.
The Advancement of Near-Zero-Waste Whole-Garment Manufacturing
The key outcome for Audren and her team was the development of a waste savings evaluation system. This data-driven approach strengthens Weffan’s position when engaging with investors and potential clients, providing concrete evidence of their technology’s benefits.
Now, for every prototype and garment design we make, we can compare waste savings to conventional methods.
Other key outcomes included:
- Creation of a product roadmap and pricing strategy
- Establishment of crucial partnerships with UK manufacturers and researchers
- Enhanced communications to explain 3D woven garment methodology to fashion brands
- Identification of the UK manufacturing market
- Development of a business model based on market research and commercial viability testing
- Improved understanding of how to integrate 3D weaving technology into existing supply chains
Overall, the study has accelerated Weffan’s journey towards revolutionising garment production in the UK fashion industry, providing crucial insights, partnerships, and systems.
This feasibility study was critical for our journey towards commercialisation. It allowed us to take the time to thoroughly research and develop our ideas and provided a safe space to explore different directions before committing to full execution.
What would Audren say to other businesses applying for funding?
Audren attributes their success to the comprehensive approach of the feasibility study, combined with the expertise of their partners and their own determination to revolutionise the fashion industry.
The systems and the management you need to write, get, and run a grant successfully can feel intensive and bureaucratic. But don’t get frustrated, you need these processes in business. They have real world application.
Download the PDF version of this case study.
Find out more about the Resource Efficiency for Materials and Manufacturing programme.