Remanufacturing office furniture: an interview with Rype Office
The Net Zero Places Innovation Network recently spoke with Dr. Greg Lavery, Director of Rype Office, about how their approach to reducing waste and conserving resources is transforming how organisations, particularly in the public sector, manage their resources. It was a fantastic opportunity for the team to hear about their latest news, developments and updates.
About Rype Office
Rype Office remanufactures office furniture to provide high-quality, eco-friendly, and cost-effective solutions for organisations across sectors. Every working day in the UK, 500 tonnes of office furniture is discarded, contributing significantly to carbon emissions. By using innovative asset management software and sustainable remanufacturing processes, Rype Office extends the life of office furniture by bringing it back to as-new condition, saving on costs, and drastically reducing waste.
About the Net Zero Places Innovation Network
The Net Zero Places Innovation Network supports local authorities with their Net Zero journey, and engages with many businesses across a wide range of sectors to support them in public sector procurement. It aims to bring the latest products and services to the forefront, to ensure local authorities are aware of the innovations being developed across the UK.
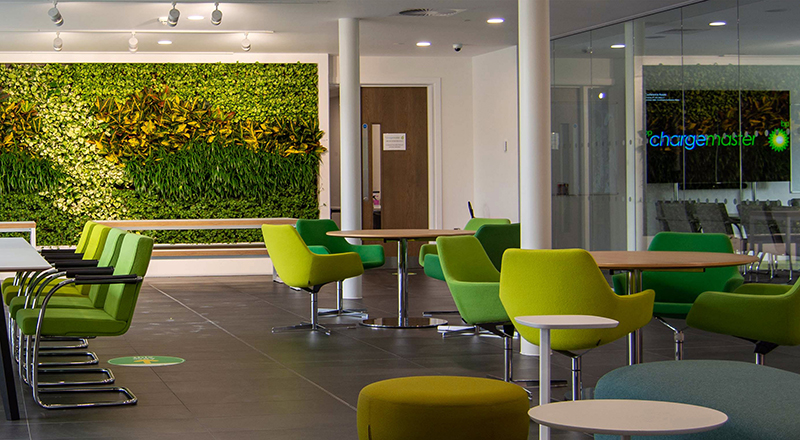
Reframing furniture management
Why is the circular economy such an important part of Rype Office’s mission?
The circular economy is essential for minimising waste and conserving resources. It focuses on extending the lifespan of products rather than discarding them after use. For example, our remanufactured furniture is the same quality as new items, but with 80% lower carbon emissions and at a much lower cost. By rethinking the traditional linear “take-make-dispose” model, the circular economy offers a sustainable and financially viable solution to reduce the environmental impact of our offices and workspaces.
Can you explain the scale of the furniture waste problem in the UK?
The scale is shocking. Every working day, 500 tonnes of office furniture is sent to landfills or recycling centres across the UK. Most people don’t know that furniture is one of the largest contributors to the lifetime carbon emissions of non-domestic buildings because it is thrown away every refurbishment or office move. This waste is largely avoidable if we reframe how we handle furniture. With better procurement, asset management and remanufacturing practices, we could significantly reduce the environmental footprint of organisations across the country.
How does your asset management software work to reduce furniture waste?
Our asset management software provides businesses with a practical tool to track, repair, and refurbish their furniture. Instead of discarding unwanted pieces, they can easily resize, recolour, reupholster, donate, or sell them. This streamlined system ensures that furniture doesn’t prematurely end up in a landfill and offers organisations a simple way to manage their resources more sustainably. All logistics are handled for the client, making it a hassle-free process. Many organisations also find the reporting functionality helpful, enabling them to track every item through every life, even after it has left them – and to calculate the carbon emissions, costs and waste saved.
Reducing carbon emissions
Remanufacturing furniture significantly reduces carbon emissions. Can you elaborate on that?
Absolutely. When we remanufacture furniture, we use existing materials, which cuts the energy required to produce new items from scratch. This results in 80% lower carbon emissions compared to making furniture from virgin resources. For example, in our projects, we deliver high-quality furniture without the environmental costs associated with the extraction and processing of raw materials. It’s a sustainable, yet scalable, solution for businesses looking to reduce their carbon footprint.
Could you share some examples of the environmental impact achieved by Rype Office?
One of our notable projects was with Transport for Wales, where we provided 77% second-life furniture for their headquarters. This project saved 90 tonnes CO2e of carbon emissions, prevented 32 tonnes of waste from going to landfills and saved hundreds of thousands of pounds. It demonstrates the tangible environmental benefits of using remanufactured furniture. We’ve done similar work with other public sector bodies like North Devon Council and Public Health Wales, helping them reduce waste and carbon output while also saving money.
Why is the circular economy particularly beneficial for the public sector?
The public sector often operates under tight budgets and ambitious sustainability goals, making the circular economy an ideal fit. By adopting remanufactured furniture and sustainable practices, local authorities and public sector organisations can lead by example. Not only can they save significant amounts of money, but they can also drastically cut their carbon emissions while ensuring that their staff have high quality ergonomic furniture to maximise their wellness and productivity. With more pressure than ever to meet environmental targets, the circular economy provides a solution that aligns with these goals while supporting local economies.
Benefits of remanufactured furniture
How do cost savings play into the decision to choose remanufactured furniture over new?
Cost savings are a major benefit. By remanufacturing furniture, organisations can achieve the same quality as new items but at a fraction of the cost. This makes sustainable choices much more accessible, especially for the public sector, where budgets can be constrained. Additionally, the financial savings don’t compromise quality—each piece we deliver is rigorously tested and remanufactured to as-new condition. Public bodies used to worry about the media and public repercussions of choosing good quality ergonomic furniture for their offices, but remanufacturing avoids this tension with its lower cost and strong sustainability credentials.
What misconceptions do you think businesses have about remanufactured furniture?
One common misconception is that remanufactured furniture is of lower quality or doesn’t look as good as new. In reality, the opposite is true because newly launched furniture often has design flaws that lead to early failures. Through choosing proven furniture and controlled remanufacturing processes, we bring furniture back to “as-new” condition. Another myth is that sustainable furniture is expensive. In fact, remanufacturing is not only more sustainable but also more cost-effective, offering savings of up to 30% compared to buying new.
How do you envision the future of office spaces with the growing emphasis on sustainability?
I believe that office spaces will increasingly incorporate sustainability into every aspect of their design, from the materials used to the way resources are managed. In fact, the new Net Zero Carbon Building Standard requires it. The circular economy will become a standard practice rather than a niche offering. As awareness grows about the environmental impacts of our choices, more businesses will seek out remanufactured furniture and sustainable solutions to reduce their carbon footprint. Our goal at Rype Office is to make these solutions as accessible and impactful as possible.
If you would like to find out more about Rype Office, or would like to speak to them please contact our expert.
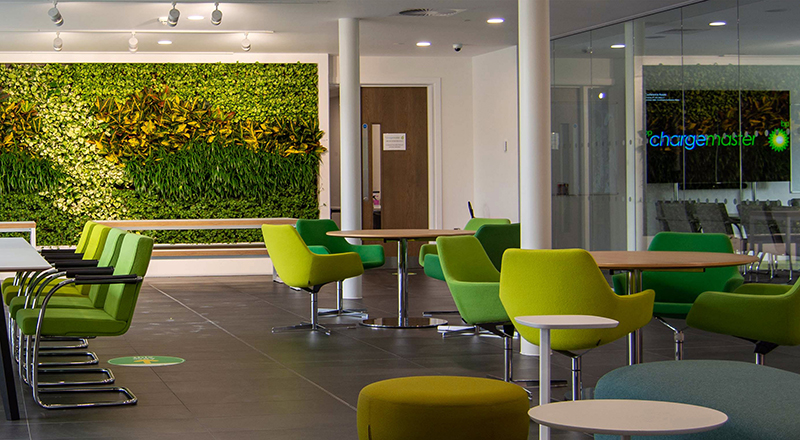
Rype Office: Adopting remanufacturing to create circular economy success
The single biggest emissions in a construction demolition project is not the building, it is the furniture.
Read more
Related programme
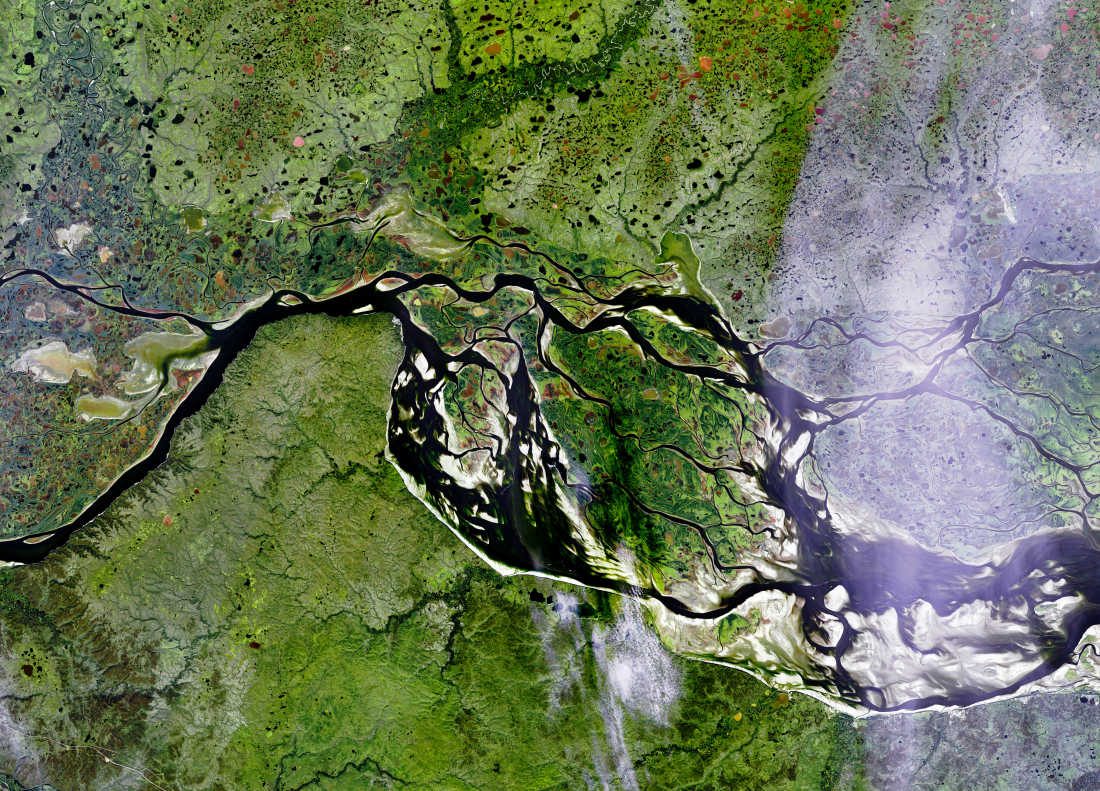
Net Zero Places Innovation Network
Making net zero a reality in the UK by supporting local/regional authorities to achieve their net zero ambitions by connecting, collaborating, sharing experiences and adopting innovation.