A cross-sector consortium has successfully demonstrated advanced computational design techniques for formulating coatings to add value to glass and metals products whilst using less materials and energy – initially focusing on antimicrobial coatings.
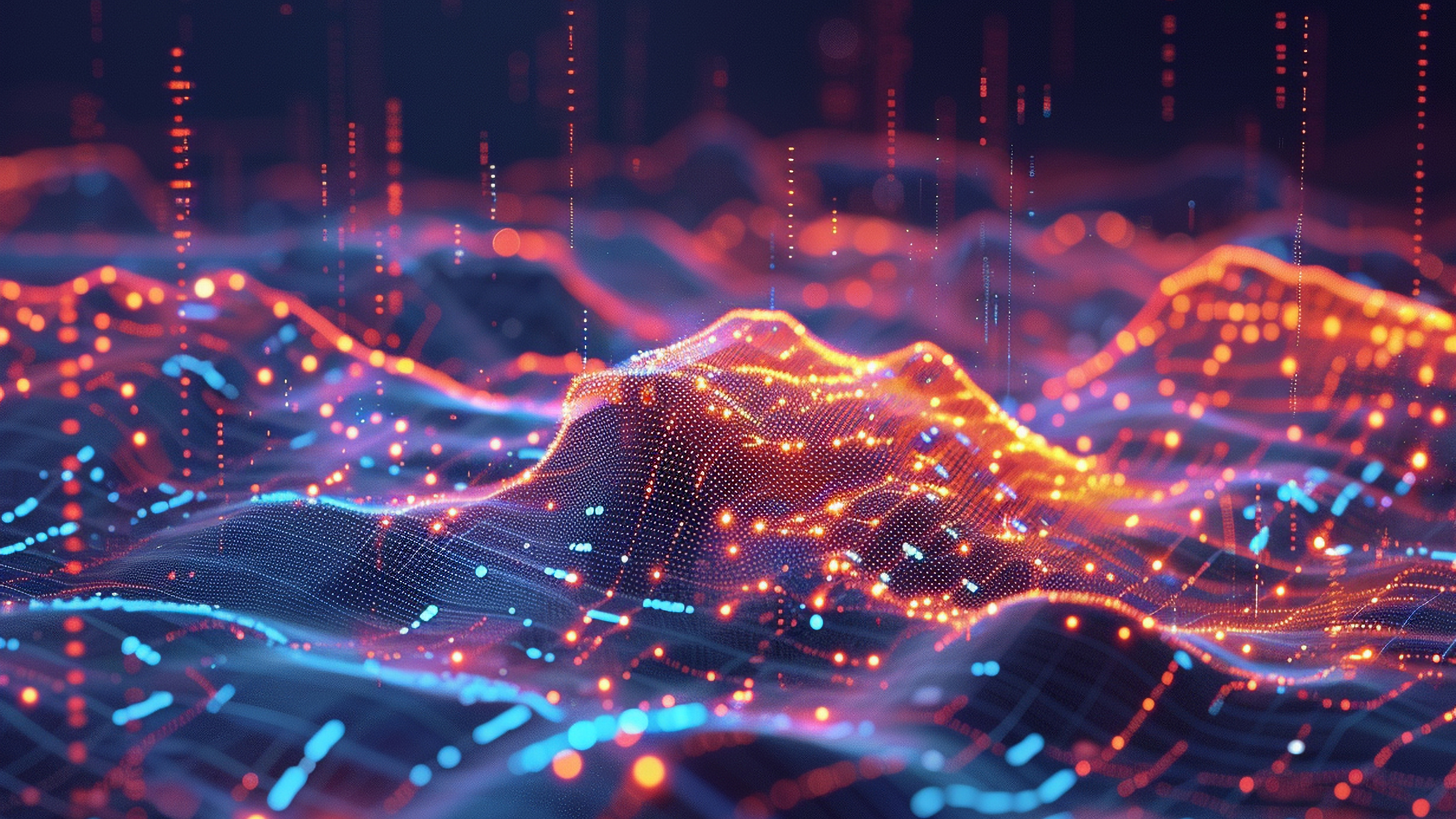
Collaborative approach
The Com2Coat consortium was led by global glass manufacturer, Pilkington Technology Management Ltd (part of NSG), and involved multiple, cross-sector collaborators: Centre for Process Innovation, Becker Industrial Coatings Ltd, Infineum UK Ltd, Spraying Systems Ltd, STFC Hartree Centre, Tata Steel UK Ltd, William Blythe Ltd. The consortium was supported by the Transforming Foundation Industries Challenge which has brought together multiple collaborative projects across the foundation industries (metals, glass, paper, ceramics, chemicals and cement).
The Com2Coat project has facilitated technology development and has given confidence that spray coating on glass and steel production lines is technically feasible and of ‘low’ risk. Innovate UK funding has been instrumental in encouraging development work to take place by enabling commercial investment decisions to be taken.
– Simon Hurst – Wet Chemistry Lead, Pilkington Technology Management Limited
Background
A functional coating is applied to the surface of a material to give it specific properties such as: corrosion resistance, thermal insulation, colouration, gloss, thermochromism, conductivity, anti-fouling, anti-microbial. For some glass and steel products, the coating can add the majority of the value to the material. As such, the development and application of innovative coatings are an important opportunity to achieving commercial advantage.
Opportunity
Advanced computational techniques are increasingly being used to allow manufacturers to intelligently design coatings which ensure higher quality, reduced consumption of raw materials, less energy consumption (when applying the coating) – and ultimately obtain a higher premium in the marketplace. It is a growth area as multiple industry sectors, such as automotive, are looking to increase product functionality, performance, and durability whilst turning innovations from concept to coating more rapidly. In a globally competitive market for glass and steel products, advanced coatings are an important opportunity for UK companies to stay competitive and provide export opportunities.
Innovative solution
The consortium took a whole supply chain view on the readiness of digital technologies to augment and enhance the traditional formulation process by leveraging cross-sector skills and technologies with non-competitive partners. Anti-microbial coating formulations were tested at pilot and product line facilities (metal and glass) and demonstrated the benefit of the computational approach to predict changes to the chemistry and/or process rather than using traditional ‘trial and error’. Spray processes and antimicrobial coatings were successfully developed giving the partners confidence that a wide range of added-value, functional coated products could be produced, i.e., antimicrobials and steel/glass is just the start. The carbon footprint of the process was also reduced as the approach is free of Volatile Organic Compounds (VOCs).
The project demonstrates the power of combining computational techniques with manufacturing production processes to add value and improve efficiency.
Impact
- Pilkington is now commercialising the technology and looking to generate sales in 2025 with exports anticipated thereafter. This involves significant capital investment which will protect manufacturing and R&D jobs in the UK and ensure that the existing manufacturing site remains profitable.
- Tata Steel is looking to implement spray technology on production lines at its Shotton site and continue working with Spraying Systems to determine how to utilise the approach for particular steel widths and line speeds.
- The success of the project illustrates the power of collaboration and the benefit of encouraging advanced manufacturing and building a higher skilled workforce in the UK.
Role of collaborators
Pilkington Technology Management Ltd (part of NSG)
Global glass manufacturer (lead partner & provided coating/process specifications and line trials).
Tata Steel UK
Global coated steel manufacturer (provided coating/process specifications and line trials).
UKRI STFC Hartree Centre
Government institute with supercomputing and data science/AI expertise (provided computational formulation approach).
Centre for Process Innovation
Technology centre and part of High Value Manufacturing Catapult (provided key physical/chemical properties of the materials and coating systems to provide the necessary data feed into activities of the STFC Hartree Centre and with Spraying Systems).
Beckers Group
Global leader in industrial paint and coatings (provided large scale antiviral/microbial coating developed by the project to NSG & Tata Steel for line trial).
William Blythe (part of Synthomer)
Leading chemical company (provided active chemicals for antiviral/microbial coating).
Infineum
Leading formulator, manufacturer and marketer of fuel and lubricant additives (provided dispersant technology for antiviral/microbial coating).
Spraying Systems Ltd
Leading manufacturer of spray nozzles and spray technology (provided expertise and optimised spray coating technology for line trials at NSG and Tata Steel).
Explore more
To find out more about other collaborative projects supported by UKRI’s Transforming Foundation Industries Challenge, delivred by Innovate UK, EPSRC and ESRC, visit: