Diversity drives innovation
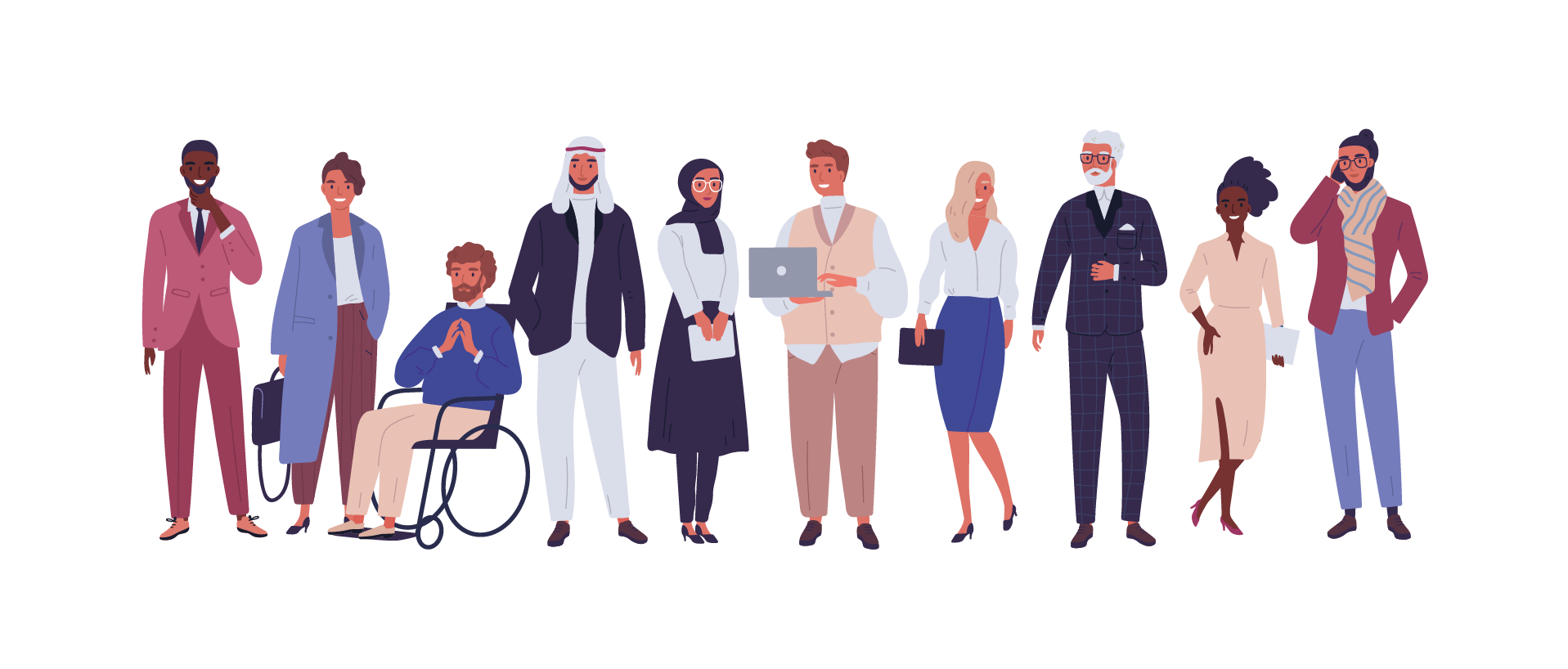
The law of unintended consequences comes into play when a simple solution is actioned to resolve a complex challenge. In the drive to be productive by reducing costs, might we be missing an opportunity to add value and simultaneously be creating flaws in our innovation system?
This article was originally published by The Manufacturer on 19th July 2021.
Imagine if there was one thing you could change that would increase the likelihood of better business outcomes eight times, your propensity for innovation and agility six times, high performance three times and double your chances of exceeding financial targets. You would want to make sure you were in on the action. This one thing is a diverse and inclusive culture: the evidence for diversity in the workplace is overwhelming.
In terms of workforce diversity, manufacturing is perhaps almost passable at a surface level: 26% of the workforce are female and 13% of the workforce are from ethnic minority groups. Ethnicity varies across sectors with only three of the manufacturing sectors having better than whole workforce average ethnic diversity. Digging a little deeper into 2020 Labour Force Survey data, it becomes apparent that representation across roles isn’t equally spread.
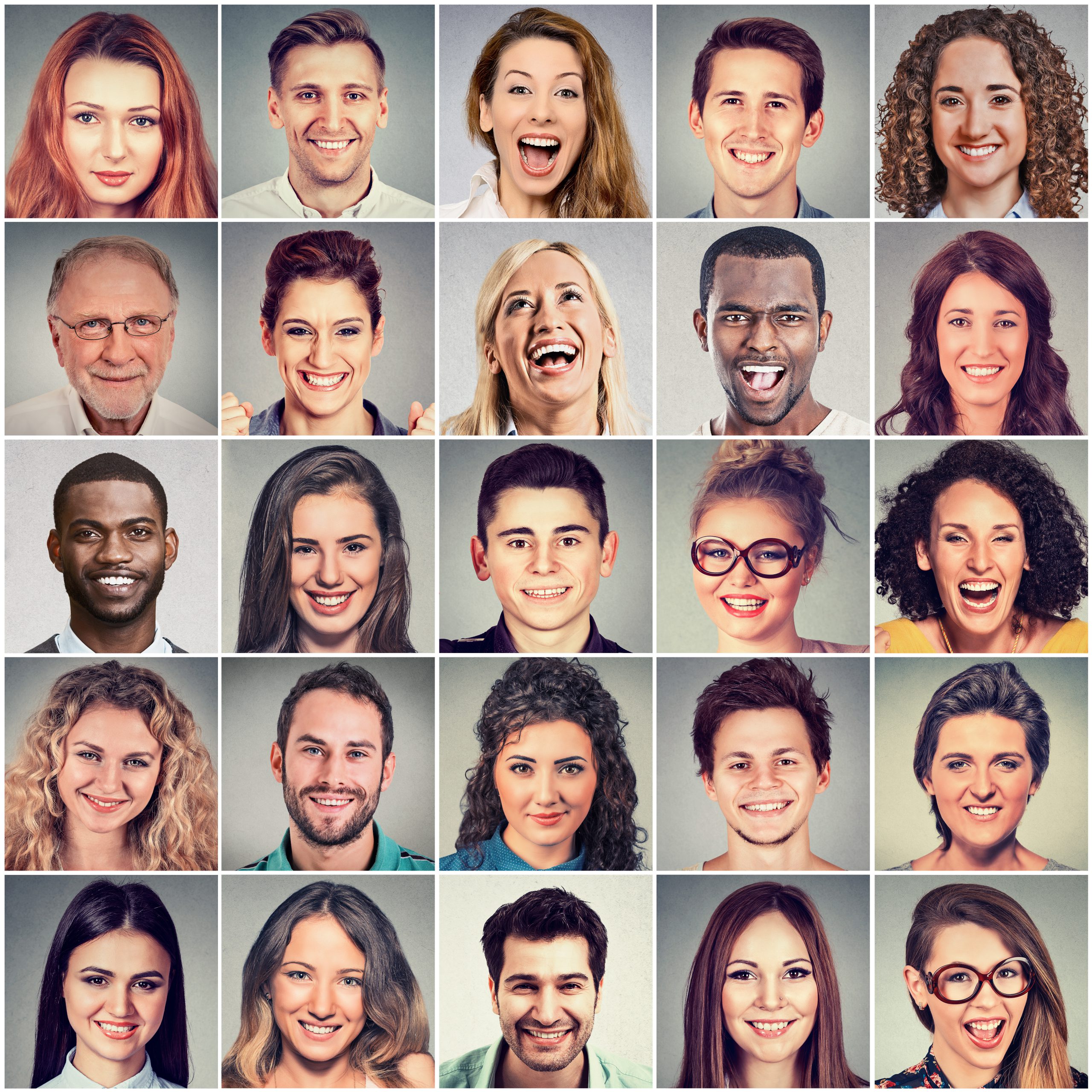
Shaping the future
A recent Inspiring Women in Manufacturing Survey of 80 women in manufacturing, undertaken by KTN in partnership with The Manufacturer, found that 57.5% felt that visible diversity within the sector would lead to a more diverse workforce. Role models from different genders, ethnicities and backgrounds, and transparency about the variety of roles, array of excellent people and mixture of the benefits manufacturing can bring (not only to the economy, environment and state-of-the-art, but also to society) is what will inspire a diverse next generation.
Impacting societal change
The same survey found that impacting societal change (employment, equality of opportunity, skills development) is significantly more important to women than either digitalisation or net zero. This is in line with findings from other sectors; men and women tend to think about innovation differently.
What does this mean for manufacturing innovation and the drive for productivity?
There is a whole range of compelling manufacturing examples of where ‘blinkered’, narrow thinking has delivered innovation outcomes that are far from optional. What is more concerning is the compounding, self-enforcing nature of the examples. Lack of diversity surely leads to less innovation?
VR headsets tend to be oversized for women who are also more likely than men to experience motion sickness when using VR4. This is not just an ergonomics issue; the way depth perception occurs differs between men and women is different but not well understood. VR systems have been developed by men for men: 51% of the potential market (women) will struggle with using the product as intended.
AI data and analytics appear agonistic. AI has the potential to displace low-skilled, administrative and secretarial jobs which are occupied by a disproportionate percentage of female and ethnic minority workers. Data on a diverse population is often missing as AI systems are constructed: what is assumed to be gender[1]neutral often isn’t – voice recognition is one example with some disastrous consequences.
Robotics and automation have great potential to improve productivity and create more high-value jobs. All good news. But equally, on the shop floor, lower-paid jobs that are replaced are occupied by a disproportionate percentage of female and ethnic minority workers. This is especially true in automotive, textiles and clothing manufacture.
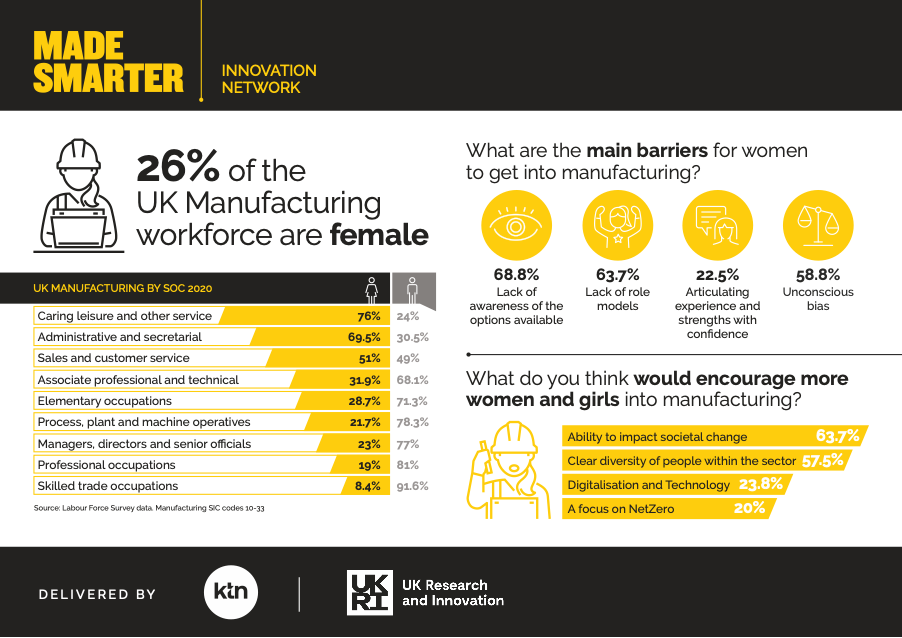
Easy targets for big impact
The profile of your workforce. Consider whether your hiring processes attract more of the same and whether you need to broaden your net. Hiring diverse teams is hiring the best – for organisational learning and innovation, the two are coupled and not mutually exclusive.
Capture data and track data on priority groups, just as you would for any organisational change. Perhaps start with intentional observation or a tally in your notebook – you might be surprised! Interrogate the data beyond the surface level. Look at how gender-age and gender[1]ethnicity intersect. Explore where different priority characteristics show up (meetings, events, decision making, networking, training, leadership) and, more importantly, where they don’t.
Find out more about the unintended consequences of technology on diversity and, in turn, innovation. Invisible Women: exposing data bias in the world designed for men by Caroline Criado Perez is a great place to start. Think about and implement inclusive design practices and carry out an assessment of the implications of your innovation. PAS 440 from BSI offers a great framework to help with this.
Safety and testing approaches – the way technologies are designed and tested for manufacturing and manufactured products needs to be more inclusive. While workplace accidents have been decreasing for men, they have been increasing for women – being excluded from PPE design considerations is just one example under scrutiny. Although men are more likely than women to be involved in a car crash, women are 47% more likely to be seriously injured in car crashes, 71% more likely to be moderately injured and 17% more likely to die9 – in part due to them being excluded from design and test considerations10.
If women don’t become more involved in the technologies developed, diversity in our manufacturing workforce will dwindle further and the cycle will compound the challenges we are facing. Now is the time to redress the balance and seize the opportunity to develop higher-value inclusive products and improve productivity in a sustainable way.
This is a call to action! Let’s spread diversity and inclusion from HR to the CTO’s office and into operations and technical design. Talk about it, measure it, track it and consider how to make sure technology development and adoption is inclusive.
If you would like to join in the conversation and help shape government thinking going forward towards positive change, or have any questions or comments, please get in touch with the KTN Manufacturing Team or share your experiences in our LinkedIn Group.
Related Content
Related programme
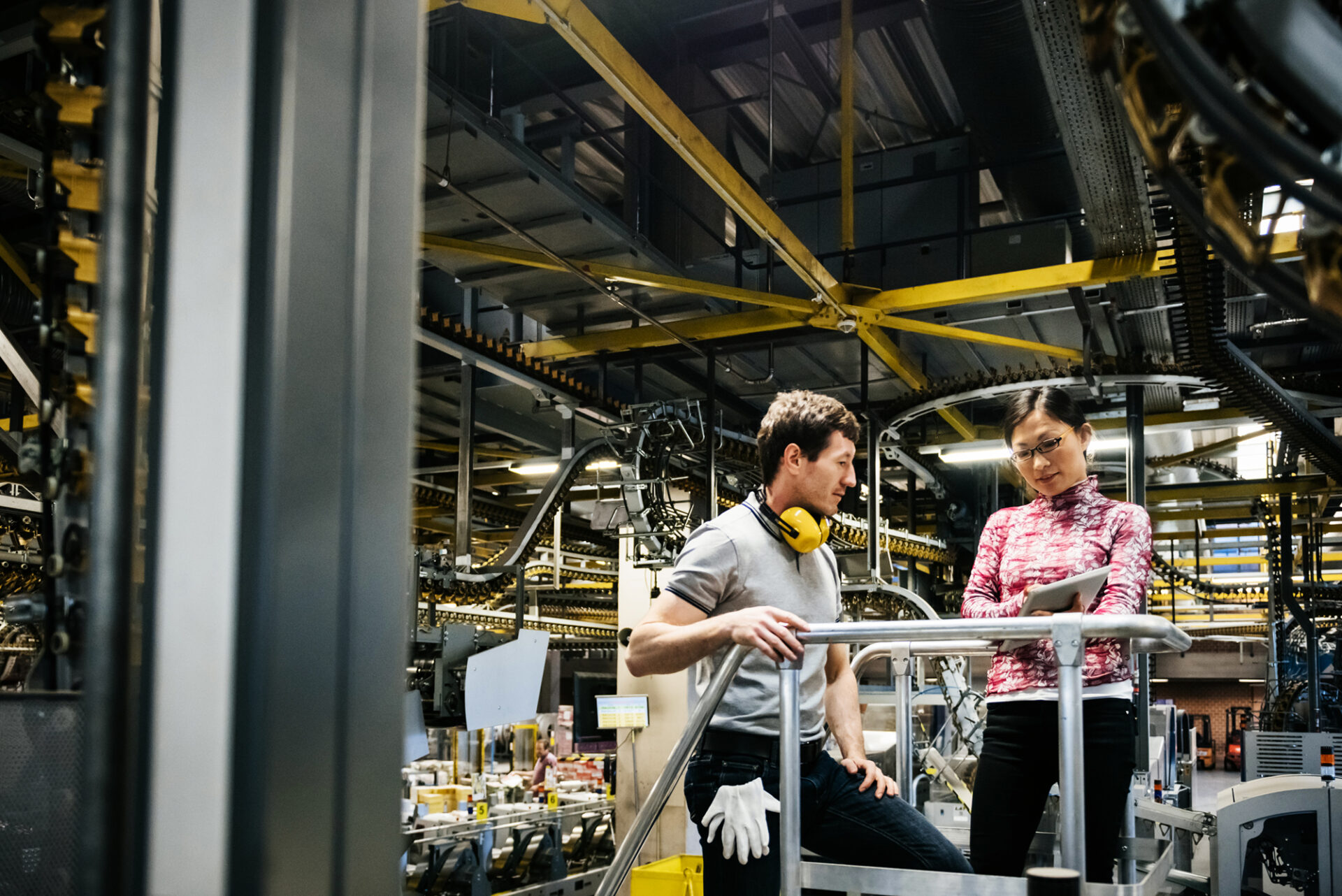
Made Smarter Innovation Network
From 2020 to 2025, Innovate UK Business Connect will be working on behalf of UKRI to join communities together to transform UK manufacturing. Join the Made Smarter Innovation Network and help us drive positive change.