Remanufacturing: five things you need to consider
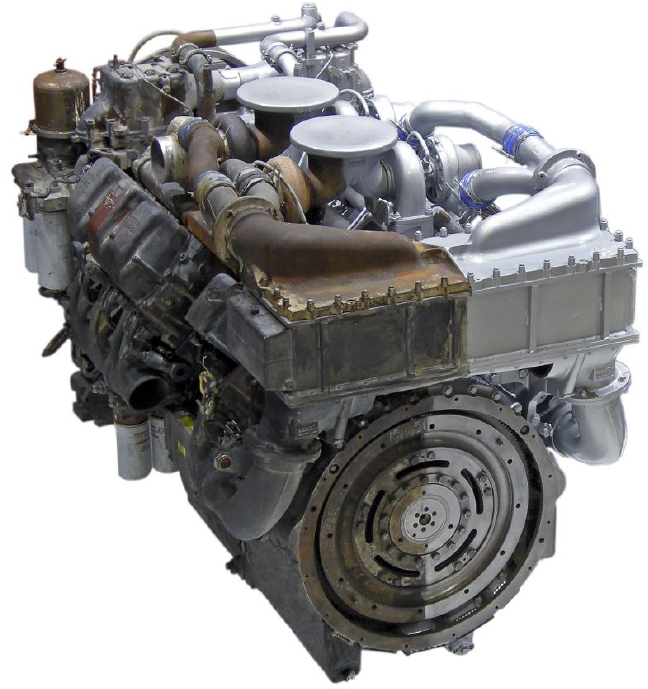
Is remanufacturing a solution businesses should be considering to meet their NetZero targets and make better use of materials?
The need to get creative and innovate around how we develop and use materials and products has never been more pressing.
NetZero targets are ambitious, the demand for rare earth metals is a potential vulnerability and, whilst we invest in alternatives, energy prices in manufacturing are high relative to the rest of the world.
To be resilient, competitive and productive we need to be considerate in how we use resources, not just with longer-term outcomes in mind but, increasingly for our businesses now.
Over the past weeks and months, the KTN Manufacturing team in partnership with Innovate UK, University of Brighton and the Department for Business Energy and Industrial Strategy have embarked on a series of workshops to explore Remanufacturing. These bring together some of the best thought leaders and practitioners in this area to facilitate discussion about the feasibility of Remanufacturing as a solution and what we, as a nation, ought to be considering next.
What is remanufacturing?
According to the British Standard 8887-220 remanufacturing is defined as the industrial practice of “Returning a product to at least its original performance with a warranty that is equivalent or better than that of the newly manufactured product”. This definition encompasses more than only end- of-life products and can refer to any product that no longer meets the consumer’s requirements.
Five things you need to consider
#1 Is remanufacturing technically feasible?
The first (and perhaps fairly obvious thing) that ought to be considered is whether or not you can return the product to a standard that as at least as good as new and, are you able to provide a warranty to this effect? The processes involved in remanufacture are likely to look quite different to the process used to produce the original product.
There is likely to be variation in the quality of the core product returned. You’ll need to be able to assess what is worth repairing and what isn’t. You might be fortunate enough to have sensor data monitoring the condition of products in-use or may need to find an effective and efficient means of non-destructive testing as products arrive on-site. At some stage, you’ll probably have to do some cleaning and, once remanufacturing has occurred, testing will need to take place. It may not be technically feasible to establish the condition with non-destructive testing to carry out remanufacturing procedures or, to obtain a like new or better standard.
#2 Does it stack up financially?
Products that are manufactured tend to be of high value. Sectors such as automotive and aerospace are most active although, other sectors are beginning to explore the possibilities. Low-value goods usually do not contain sufficient value or margin to make remanufacturing worthwhile. There are some notable exceptions, for example, printer cartridges, where the remanufacturing process is relatively simple and low cost and the variation in core condition is minimal.
Products are likely to be returned for remanufacture in a variety of states. Efficient and effective ways of establishing the condition of the product (is it worth investing effort in repairing?) will be fundamental to a financially variable proposition. How will you deal with the products that can’t be manufactured? How will cash-flow work?
Remanufacturing usually requires investment in new technology, processes and skilled labour. This upfront cost means risk and ROI needs to be well understood.
# 3 Does it make sense environmentally?
On the face of it, keeping a product in use for longer seems like an eminently sensible thing to do from an environmental perspective. It is worth considering the energy and emissions that are embodied in the product through remanufacturing. How does this compare to manufacturing original equipment? Also, what energy and emissions are embodied in the product through its new life? Would an updated release of the original product be more energy-efficient or release fewer emissions? Perhaps this is something you can address as you improve on the original.
# 4 Does the business model work?
Remanufacturing often goes hand-in-hand with business model innovation. Servitisation models, for example, offer the benefit of more control over the whole product lifecycle: the design can be optimised, maintenance and servicing cycles can be optimised and, use be monitored through life.
The stability and volume of core product supply must be considered. Some business models thrive a steady stream of the core product (engine blocks, for example) whilst others cope best with batches. The practicalities and economics of reverse logistics can have a significant bearing on what is feasible. Whilst it can often be a hurdle in terms of the viability of remanufacturing, it can also be a driver for innovation. Remanufacturing tends more prevalent with goods sold and returned through B2B models than B2C.
# 5 Is there sufficient demand for remanufactured products?
Customers often perceive remanufactured products as lower value, even when the warranty exceeds that of a new product. Consequently, they expect to pay less.
The value to customers must stack up: either in terms of lower costs or additional benefits that offer sufficient incentive (better performance, for example). Understanding what motivates your customer is key.
Procurement channels can often be stifling. Although these can present a significant hurdle, overcoming these barriers can be a huge opportunity for a business.
What’s next?
At KTN, we’ll be continuing our work with Government and thought leaders to explore what more can be done in this area. If you’d like to have input or are keen to explore remanufacturing or circularity in your business, please get in touch with the manufacturing team at KTN. We’d love to hear from you.
Whether it’s remanufacturing, recycling, reuse or re-design for better energy efficiency, lower emission and less material use (throughout the products lifecycle) we can help you explore different options and make connections to thought-leaders, practitioners, technologies and researchers.
To stimulate thinking on the topic, you might find our ‘30 ideas for circular economy’ card set useful.