Breakthrough materials remove excess sound from your environment
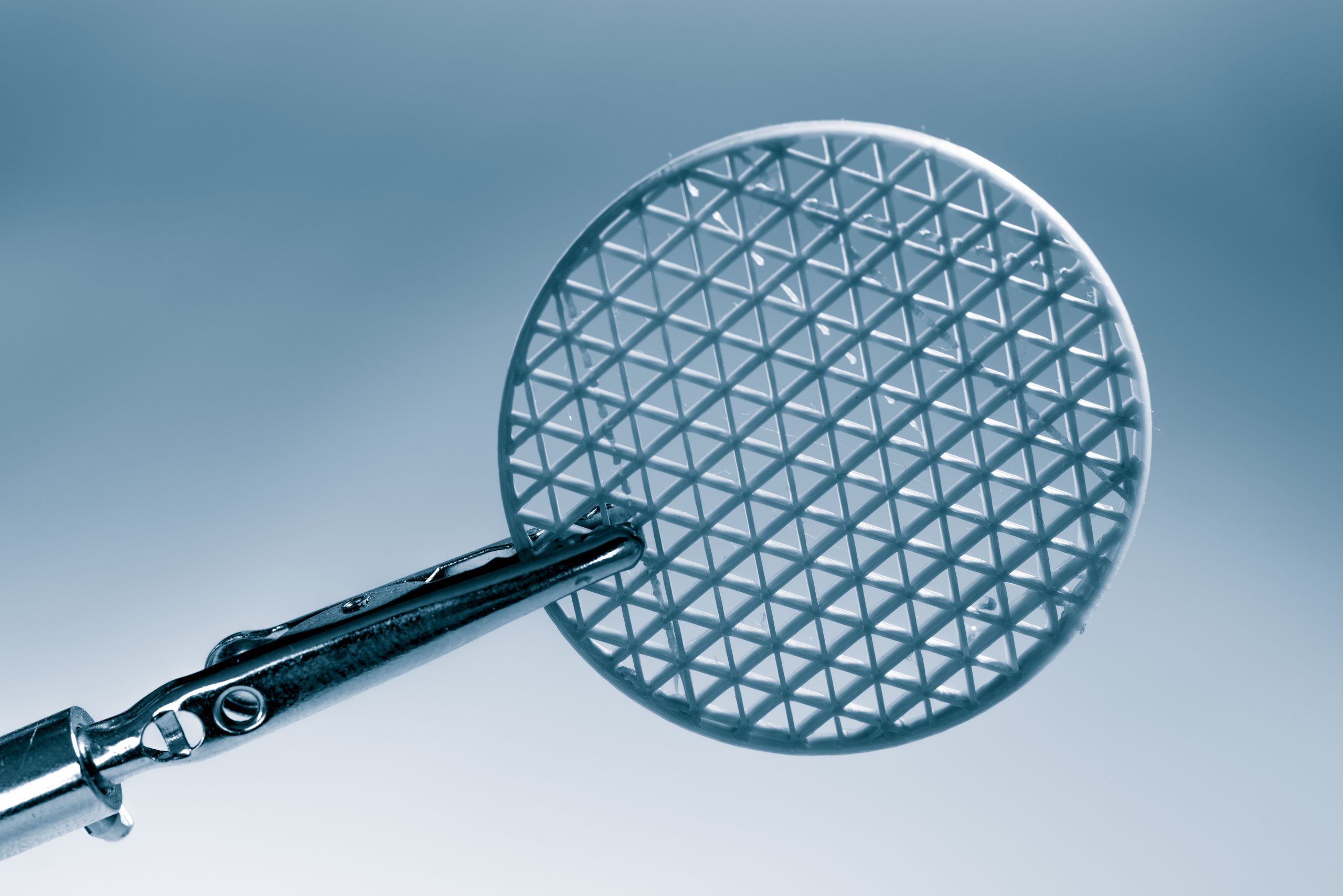
Recently Bill Gates has invested in metamaterials. In this article, we look at the successful commercialisation of acoustic metamaterials and try to understand how we might move other metamaterials from the laboratory into commercial applications.
As a part of the activities of the Metamaterials Innovation Network in its aim to commercialise metamaterials, we asked Professor Gianluca Memoli from the University of Sussex and founder of Metasonixx Ltd, a start-up specialised in acoustic metamaterials solutions, to share his thoughts and expertise in commercial success of acoustic metamaterials.
What is so special about acoustic metamaterials?
In the metamaterial arena, acoustic metamaterials were the last ones to arrive on the scene. The first paper to use this name only dates to 10 years ago. However, over the years, they have been used all over the acoustic and vibration spectrum, from medicine to seismic waves and from noise management to precise sound delivery without headphones. They can be used to bend sound around corners, to perform noise cancellation without headphones and to deliver two different programmes to passengers and drivers in a car. It is therefore not surprising that market forecasts predict that acoustic metamaterials will soon catch up with their optical counterpart and eventually share 50% of the market in 2030.
What are acoustic metamaterials actually made of?
In my experience: any normal material. My team made acoustic lenses to be used in air from wood, paper, plastic, metal… and more recently, rubber. The choice of the bulk material is obviously more limited for metamaterials to be used underwater, but the key point is that it is the geometry that does the trick. In the optical case, a recent Nature paper has demonstrated that at least two different materials are needed to create a metamaterial antenna… But, in acoustics, one of the materials is already available: it is the one through which sound moves. Just like composite materials, acoustic metamaterials are a success of engineering and user-centred design: two disciplines where UK companies excel.
I have seen a lot of 3D printed samples, with different geometries that are often also nice to see. Is 3D printing the way metamaterials will get into our homes?
Advanced manufacturing (3D printing) is quite expensive, with prices that start at £1000/m2. This is not affordable for a small company or for the end consumer. We know that KEF UK has pioneered injection moulded metamaterials for its loudspeakers, while SonoBex (another UK company) has used metal casting for its narrow-band noise barriers. Other companies, like Metasonixx, have been looking at these techniques and others, like die casting and vulcanisation. Scale manufacturing is the key to exploiting acoustic metamaterials. Nationally, we would benefit from a facility where the different techniques can be tested.
What other barriers do you see for metamaterials to be adopted?
This question has been addressed in a recent KTN meeting and some hypothetical answers have been debated. We need compelling demonstrators that would turn visionary companies into adopters. But, we also need a dedicated metrology: how can we compare existing products with their metamaterial counterparts, in a brochure, when existing ISO standards do not seem to work? Having worked at the National Physical Laboratory, this aspect is close to my heart. At Metasonixx, we have seen an extreme case: a panel that clearly reduced noise but that, according to standard measurement techniques, did not work just as well. Metamaterials are no longer homogeneous: they need punctual techniques. But more importantly, we need to prepare the next generation of entrepreneurs. It is time for metamaterials to go out of laboratories and enter our everyday lives.
Why did you start working at Metasonixx?
A lot of start-ups are born when a group of friends meet in a pub and dream of changing the world. In my case, I wanted to get back “control on sound, the same control we have on light”. I remember singing this motto to the notes of Imagine by John Lennon, a couple of years back. I worked hard on this through my fellowship but then realised that if I wanted people to benefit from my research, I needed to take a step further: we needed a company. And Metasonixx was born. It now employs two engineers and we recently designed some panels to help noise management in noisy hospitals. In 5 years, we imagine lightweight panels in open offices and people’s homes.
Is noise management the only application for acoustic metamaterials?
In a recent survey, I asked the members of my SIG to highlight the key applications for acoustic metamaterials. They pictured a future where metamaterials are used to shape acoustic energy as the norm. But the technological advancements they wanted to see most are in the area of directional sound and actuated metamaterials. For my academic research, this means putting an acoustic object in front of a speaker or a microphone, to make an acoustic projector or an acoustic camera look just like their optical counterparts. But, it also means creating sound on demand, both underwater and in medicine. As my colleague Fabrizio Scarpa was saying in a previous article, the collaboration between academia and companies is key to this success. This means that realities like KTN, which kindle these collaborations, are key to the success of the UK metamaterials community.