The importance of collaboration between academics and industry for commercialising metamaterials
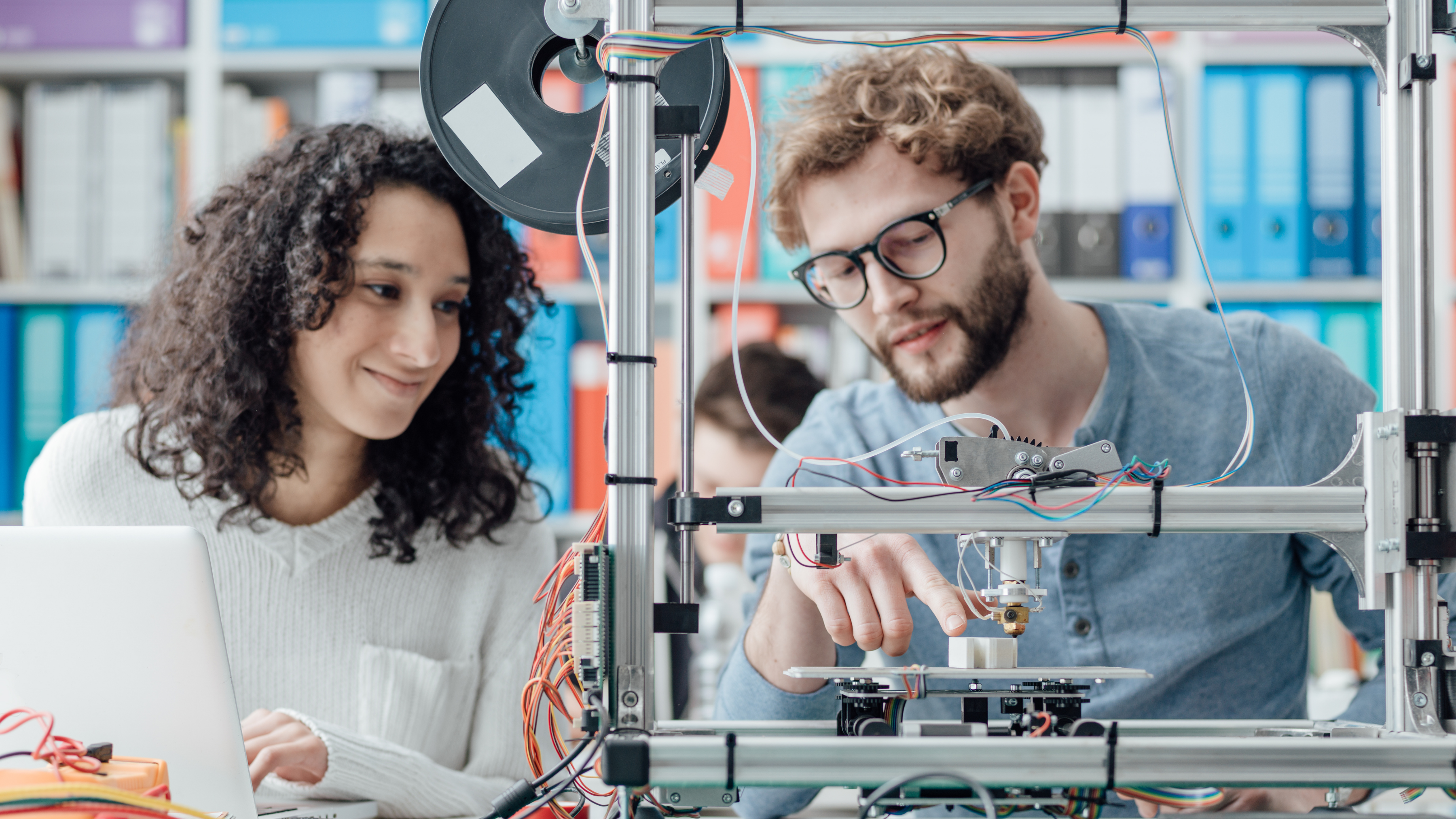
In this article, we go over the strong case for academics and industry working together on finding solutions through metamaterials
As part of the activities for the Commercialising Metamaterials Innovation Network, we asked Professor Fabrizio Scarpa from University of Bristol to share his experiences and insights of working closely with industry.
Why is this sort of collaboration key?
Mechanical metamaterials are typically developed by engineering specific “anomalous” equivalent properties. Typical examples are negative Poisson’s ratio, negative and zero thermal expansion and negative stiffness/compressibility. Those unusual properties need to be designed from the onset, and it is often necessary to integrate manufacturing and performance metrics already at the conceptual phase of the development to obtain the mechanical metamaterial sought after. From my experience, this synergy is quite useful for having industrial partners and end users involved from the beginning to develop fit-for-purpose mechanical metamaterials.
What are some personal examples of this collaborative work?
Kirigami is the ancient Japanese art of cutting and folding paper. Kirigami techniques can actually be virtually applied to any material substrate, be a metal, a thermoplastic or a thermoset composite. We have developed general techniques to couple the development of Kirigami patterns with modular moulding to generate complex three-dimensional cores and shapes using composite materials. In a project with a major aerospace OEM we were requested to develop composite cores with special zero curvature, negative stiffness and adaptable to complex shapes, using both thermoplastics and thermoset materials. The cores could not be simply printed by additive manufacturing, so from the beginning we involved the industrial customer to provide specific design constraints and requirements in terms of their in-house tooling and manufacturing processes. Those constraints allowed us to iterate a design and manufacturing route together that allowed to achieve the performance metrics and a product that was mostly fitting the business model of the industrialist. The concept is currently developed at higher TRL for a different application that potentially could be more revenue-generating.
Negative Poisson’s ratio materials and structures are currently quite popular for sport, biomedical and footwear applications. In the past we developed a concept of hybrid padding using combinations of our auxetic (negative Poisson’s ratio) foams and lattice structures for supporting the back and torso of patients with posture disabilities. While the concept may work very well in theory, the large design space available for these hybrid structures in terms of manufacturing parameters, properties and final shape make almost compulsory the involvement from the beginning of end users and service providers to create a mechanical metamaterial that is both performing and usable in a real context. We have partnered up with NHS, charities of end users and companies in the supply chain to integrate all the design aspects of those auxetic metamaterials to make a padding fit for purpose for the specific needs of the patients. We were also able to integrate some added multiphysics functionalities to those materials, because of the remote healthcare requirements the charities did ask later to incorporate into the design. The latter aspect is quite important: it allowed us to develop a concept of blue sky active auxetics by simply implementing in a collaborative way the desiderata of our partners.
How can academics approach industry?
I would encourage academics to get involved from the beginning with industrialists in shaping families of metamaterials. Product design, materials selection and architectures are important aspects of the metamaterials paradigm. A strict collaboration with an industrialist or end-user from the beginning may lead to better products that are realistic in a general technological landscape. Some of the most critical comments I heard over the years about metamaterials is that they often seem a solution in search of a problem. By involving industrialists at early stage, the academics can better define the scientific design space and provide a concept fit for purpose. Contacts with relevant industrialists may be difficult, however over the years workshops organised by KTN on materials, manufacturing processes and specific end-users communities have provided some good opportunities for connection. My personal experience is also positive on finding contacts and exchanges via professional social media. Current Catapult Network workshops can also provide a way for contacts and collaboration. KTN’s Commercialising Metamaterials Innovation Network is a great opportunity to make interact academics interested to further the TRL of their concepts with relevant industrialists.
At what stage in their research should academics make connections with industry?
There is a tension between the development of a metamaterial concept that satisfies a pure scientific curiosity and something that could be also used for more practical applications. My personal experience from collaborating with industry is that, if you use the NASA TRL scale, you will need to have those industrialists already involved at TRL 2 and onwards to create a metamaterial with a realistic perspective of future industrial development. The TRL 4-6 “valley of death” is sadly very much present in the field of metamaterials, and the earlier the engagement of the industrialist, the better the chances of getting the metamaterial right and its rate of survival.
Become a part of the dynamic Commercialising Metamaterials Innovation Network today!