Innovation Exchange challenge: Automated separation of permanent magnets from vehicle motor drives
EMR are looking for time and cost effective ways to automate motor disassembly, and efficiently separate permanent magnets and copper coil from rotor housing.
Opportunity Details
When
Registration Opens
30/11/2023 00:00
Registration Closes
24/01/2024 17:00
Award
Successful projects will be awarded up to £25k over 3 months to explore their solution with the challenge holder with the possibility of further adoption upon successful trials.
Challenge background
EMR are the largest UK end-of-life vehicle recycler. In the recycling process, the whole vehicle is shredded. Most of the components have a route for recycling, and the drive motor can be collected, the copper coils and rotor disassembled and magnets manually stripped out; however, it is not economic or practical to separate the parts in this way.
There is a need to develop an automated disassembly process which would separate the rare earth magnets from the rotor. This would allow for these permanent magnets to be recycled and materials to be integrated back into the supply chain, reducing reliance on virgin materials and geopolitically sensitive global supply chains.
The magnets are made from rare earth elements that are classified by the UK as Critical Minerals. Critical minerals are fundamental to pretty much everything we do. e-mobility is an important market with an increasingly heavy demand for critical materials; for example, there is an average of 5kg of rare earth magnets in a Battery Electric Vehicle that if recovered, could contribute to the UK’s security of supply through circularity.
Challenge requirements
EMR are looking to find/design an automated disassembly process which will allow them to process 25,000 drive motors next year, and up to 200,000 drive motors per year by 2030. Working with the Challenge Holder the solutions provider should aim to develop a process which allows for the safe and economical separation of rare earth magnets embedded in an electric vehicle drive motor.
The solution should be able to process electric vehicle drive motors, ideally as complete units, as removed from an end of life vehicle. These will vary hugely in nature and are not standardised.
Any disassembly work which can recover additional materials other than the magnets (eg copper windings, the steel rotor) during the process are of interest but not critical to this application.
The solution should be suitable for operation in an industrial environment, processing used, end of life drive motors.
Eligibility
Entrants to this challenge must be one of:
- a UK registered business of any size
- a academic institution
- a research and technology organisation (RTO)
Your project must:
- have a grant funding request up to £25,000
- last up to 3 months
- carry out its project work in the UK
- intend to exploit the results from or in the UK
Rewards & Market Opportunity
Selected applicants will be given an opportunity to pitch (virtually) to EMR. Successful solutions from the pitch day will be awarded up to £25k over 3 months to explore their solution with EMR with the possibility of further adoption upon successful trials.
The benefits package for a successful applicant may also include:
- Support from Innovate UK KTN
- Support in the development of a prototype or pilot
- Technical support
- Invitation to attend or present at KTN events
- A potential business collaboration
- Investor introductions (if investment is required)
- Support if any Innovate or similar competitions are relevant.
Related programme
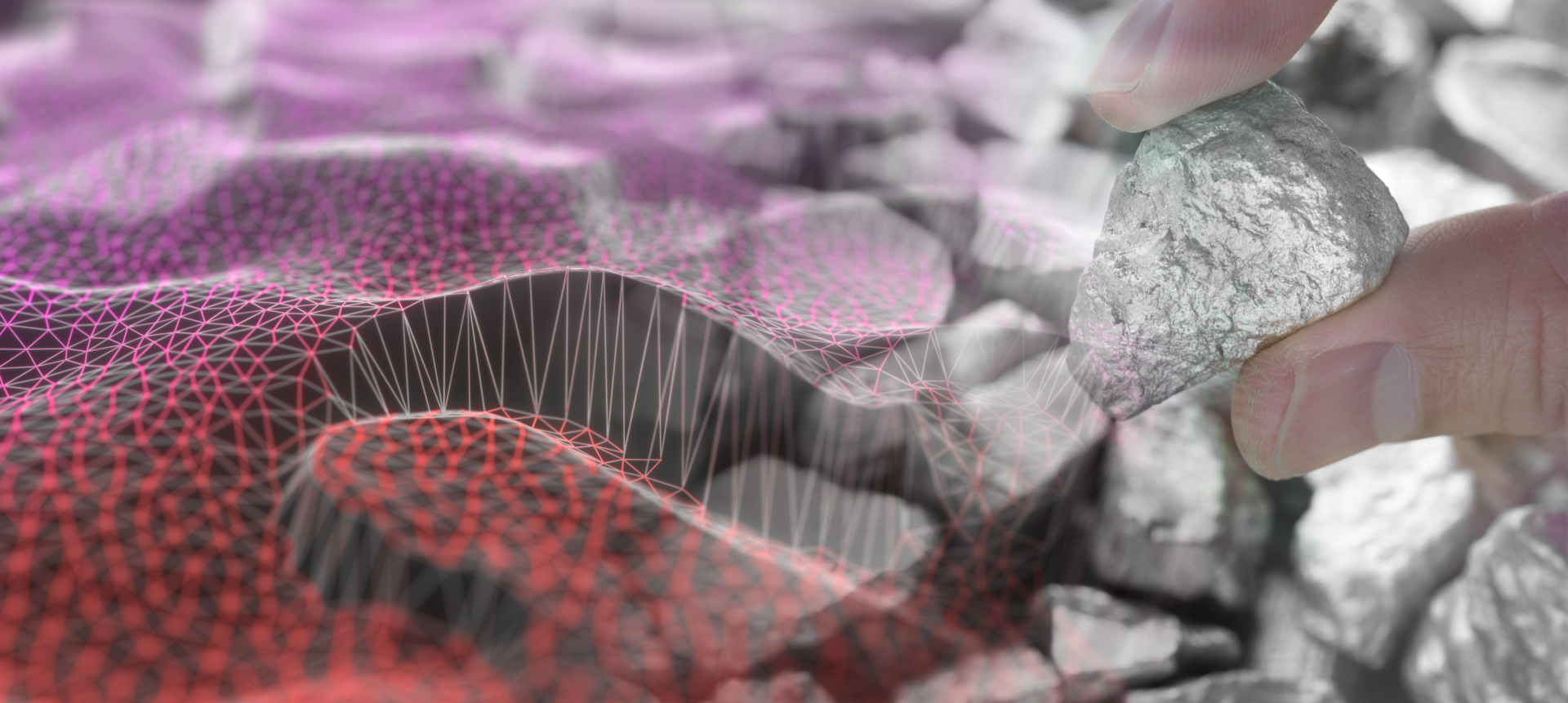
Circular Critical Materials Supply Chains
This £15 million programme will support the development of resilient UK based supply chains for rare earth elements, with a focus on primary (mine to magnet) and secondary (End of Life to magnet) supply chains.