Sustainable Aviation Fuel: Power-to-Liquids
The UK Government launched their Jet Zero Strategy in 2022, setting out how to achieve net zero aviation by 2050. Sustainable Aviation Fuel (SAF) is one of six key measures outlined in the strategy and a mandate will be introduced in 2025 to deliver at least 10% SAF in the UK jet fuel mix by 2030. Currently most of the SAF provided in the UK is derived from waste oils via the HEFA process1, as it is the cheapest route, however, to meet Government’s target, a portfolio of feedstock and production pathways will be required. Power-to-Liquids (PtL) is one novel production route being developed.
What is Power to Liquids?
SAF refers to the blend of a synthetic component and traditional jet fuel (kerosene). There are seven approved technical pathways to produce the synthetic blend component (SBC). The PtL pathway is currently only approved for use at up to 50% blend. The process to produce the SBC, via PtL, is not a single process step, it requires a combination of technologies. Some processes, like Fischer Tropsch (FT), hydroprocessing and electrolysis are commercial and deployed at scale, but reverse Water-Gas-Shift (r-WGS) and carbon capture processes are less well developed.
We have a strong conviction that the future requires a myriad of solutions that will work in parallel – for Airbus, PtL is essential and we are committed to supporting the development of PtL fuels to scale as quickly as possible to meet global demand.
– Solange Baena, Airbus
Technical challenges
Hydrogen production
At present, the primary method of hydrogen production utilises fossil fuels, via methane steam reforming.
CH4 + H2O –> 3H2 + CO
To be truly low-carbon this process needs to be coupled with carbon capture, and when it is, it is often referred to as ‘blue hydrogen’. However, energy sources including nuclear, solar and wind power, are increasingly being used to produce hydrogen via water electrolysis, referred to as ‘green hydrogen’ to achieve maximum GHG savings.
2H2 O+e− → 2H2 + O2
Water electrolysis can be carried out using various electrolyser technologies which are commercially available, each with their own advantages and disadvantages;
- Alkaline (AEM) electrolysers offer a low overall H2 production cost, with low capital costs, but significant costs to maintain. The electrolyte solution is corrosive and the electrodes can have a short lifespan, requiring frequent replacement.
- Polymer Electrolyte Membrane (PEM) electrolysers offer high durability and are capable of managing a flexible power input. The electrodes typically use materials such as iridium and platinum which can make them expensive and sensitive to water impurities, however this means that they can produce very high purity hydrogen.
- Solid Oxide electrolysers offer high electrical efficiency and can be optimised on a system level, they are tolerant to impurities and produce high purity hydrogen, but they work at high temperatures and are not currently commercially well developed.
Carbon dioxide capture technologies
CO2 is the main carbon feedstock for PtL derived fuels. Using CO2 captured from the air or from a CO2 source (such as a power plant or industrial process) can offer a reduction in the overall lifecycle carbon emissions of the fuel due to closing the carbon cycle. CO2 from Direct Air Capture (DAC) is very attractive, it allows a closed loop carbon cycle but the technology is not yet mature and expensive. Point source CO2 capture from industrial clusters and/or energy intensive industries offer a much more concentrated CO2 stream which enhances the capture kinetics.
There are several chemical technologies to capture CO2 from either point source or direct air capture. Again, these each have advantages and disadvantages:
- Liquid amines are regularly used for capturing contaminants from industrial waste streams, these are highly corrosive and processes can generate significant amounts of solvent waste.
- Ionic Liquids have high thermal stability, and are more recyclable, however they are expensive.
- Solid based sorbents, including a diverse range of micro and mesoporous materials, can overcome the high energy requirements of liquid technologies, but have lower capacities.
- Molten carbonate fuel cells are becoming an attractive option for carbon capture as they produce heat, power and/or hydrogen, however component durability remains an issue.
Catalytic technologies
Reverse Water-Gas-Shift (r-WGS) Catalysis
CO2 + H2 <–> CO + H2O
r-WGS is the least mature process and uses a catalyst to convert CO2 into CO to allow it to undergo further reaction. r-WGS catalysts are typically comprised of a well dispersed metal (Cu, Ni or pgm) supported on a metal oxide support. Research into more selective catalysts is needed to suppress undesirable side reactions and more durable catalysts that are better able to tolerate hydrothermal ageing and coking.
Fischer-Tropsch (FT) Catalysis
xCO + (2x + 1)H2 <–> CxH2x+2 + xH2O
Developed in 1925 and rigorously optimised since, the FT process converts the mixture of CO and H2 into liquid hydrocarbons (C6-C18 is suitable for synthetic jet fuel) and is the most mature technology of the PtL processes. Catalysts are comprised of an active metal chosen from Co or Fe deposited on an oxide support such as Al2O3 or a zeolite. Promoters such as silica and potassium can be added to help with reduction and hydrocarbon selectivity.
Combined r-WGS and Fischer-Tropsch Catalysis (direct CO2 conversion)
Recent developments have been focused on the combination of the r-WGS and the FT catalysts into one system using a multifunctional hybrid catalyst; eliminating the separate, energy intensive r-WGS shift reactor. This allows for an overall reduced capital cost and lower environmental impact. However, this process is in an early stage of maturity, and there is scope for optimisation through process engineering and catalyst development.
Post processing and after-treatment
After the long chain hydrocarbons have been produced, they require separation and, in some cases, further processing to give a drop-in synthetic blend component. Processes include hydrotreating, cracking, and isomerisation.
With the development of next generation catalysts and process engineering opportunities, along with the decrease in hydrogen production cost that is already being realised, the PtL route could provide a promising pathway to lower cost, lower environmental impact synthetic jet fuel.
– Prof. Mohamed Pourkashanian OBE
Feedstock and energy demand
One of the challenges in developing PtL processes is securing sufficient low-carbon hydrogen and CO2. In 2019, the demand for aviation fuel was 14.7m tonnes. The UK SAF mandate proposes that in 2030, 10% of the annual UK jet fuel demand will be derived from sustainable feedstocks, with a PtL subtarget, (in a high uptake scenario) of 0.2%, requiring the below requirements feedstock quantities:
- 88,000 tonnes water
- 14,000 tonnes hydrogen
- 100,000 tonnes CO2
The UK’s ambition is to produce 5GW of electrolytic hydrogen (equivalent to 0.75m tonnes) and capture 5m tonnes of CO2 by 2030. If 0.2% of the total aviation fuel used in the UK were to be produced by the PtL route, it would require ~2% of the UK’s total low carbon hydrogen production and 2% of the captured CO2. 1kg of green hydrogen production via electrolysis requires 10kg of fresh water, increasing the demand on water as a feedstock. For every mole of hydrocarbon formed through the FT reaction, a mole of water is also produced. This water could be recycled and used for electrolysis, but this is not sufficient, and additional water would be required.
Conclusions
The PtL process offers the UK a carbon neutral route to produce sustainable aviation fuel, but large-scale deployment is economically and technically challenging. There are still significant hurdles to overcome – from catalyst development and process integration but also in securing enough feedstocks (carbon and hydrogen) and energy – to make the process technically viable at scale.
The UK will need to invest in low-carbon grid energy capacity, and support energy storage or nuclear options to provide the continuous supply of electricity required to support the high energy demand for low carbon hydrogen production, DAC and SAF production and post processing. Fortunately, the UK is well placed to address these challenges by leveraging knowledge and expertise in technology development and by building on its strong renewable energy industry to bring PtL technologies to scale.
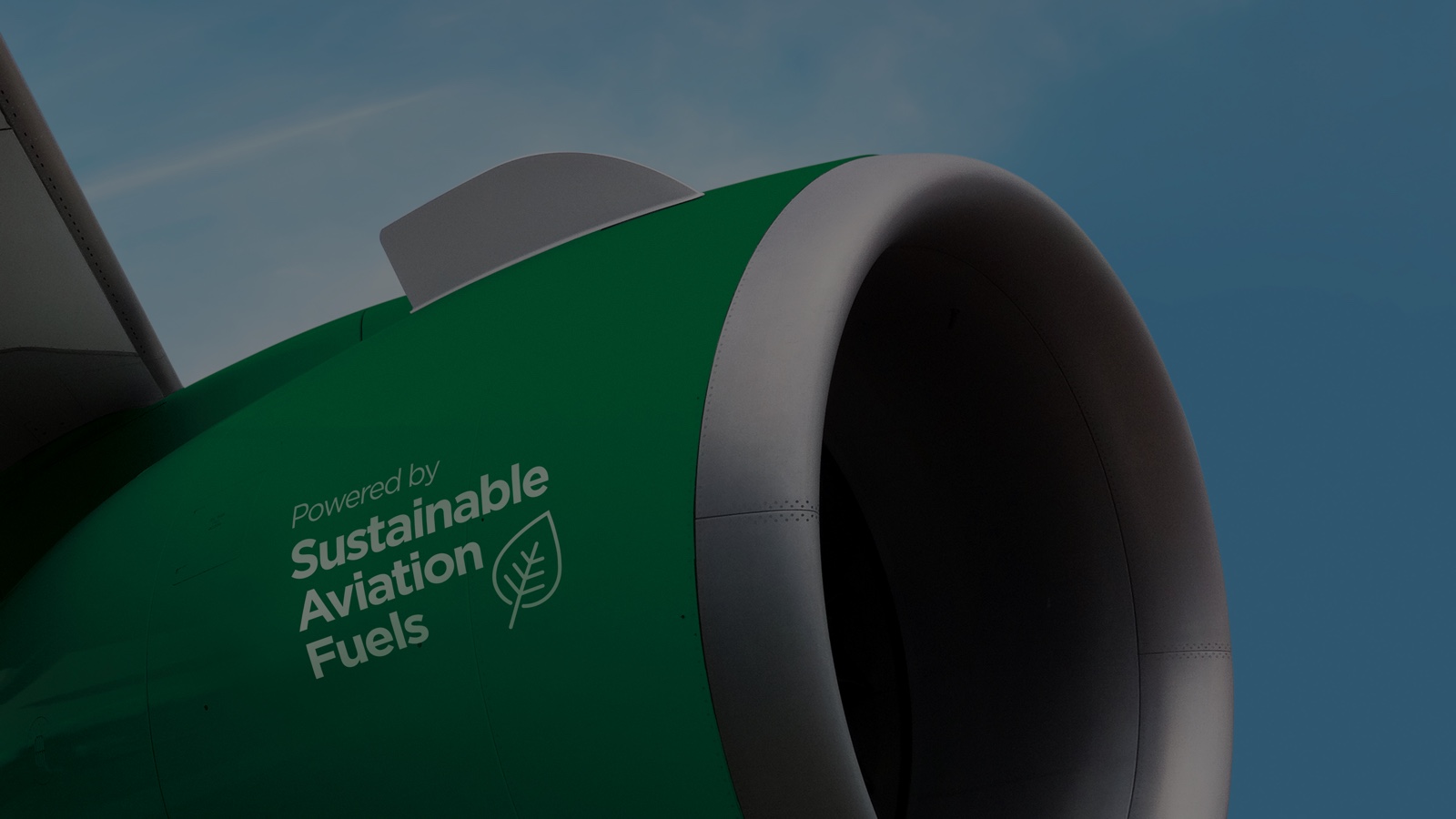
Power-to-Sustainable Aviation Fuel event recording
This online masterclass represents a valuable opportunity for experts in different parts of the supply chain to share interest and knowledge around the potential for SAF via PtL, exploring technical challenges and opportunities to build a UK supply chain.
Read more
Our Experts
Related programme
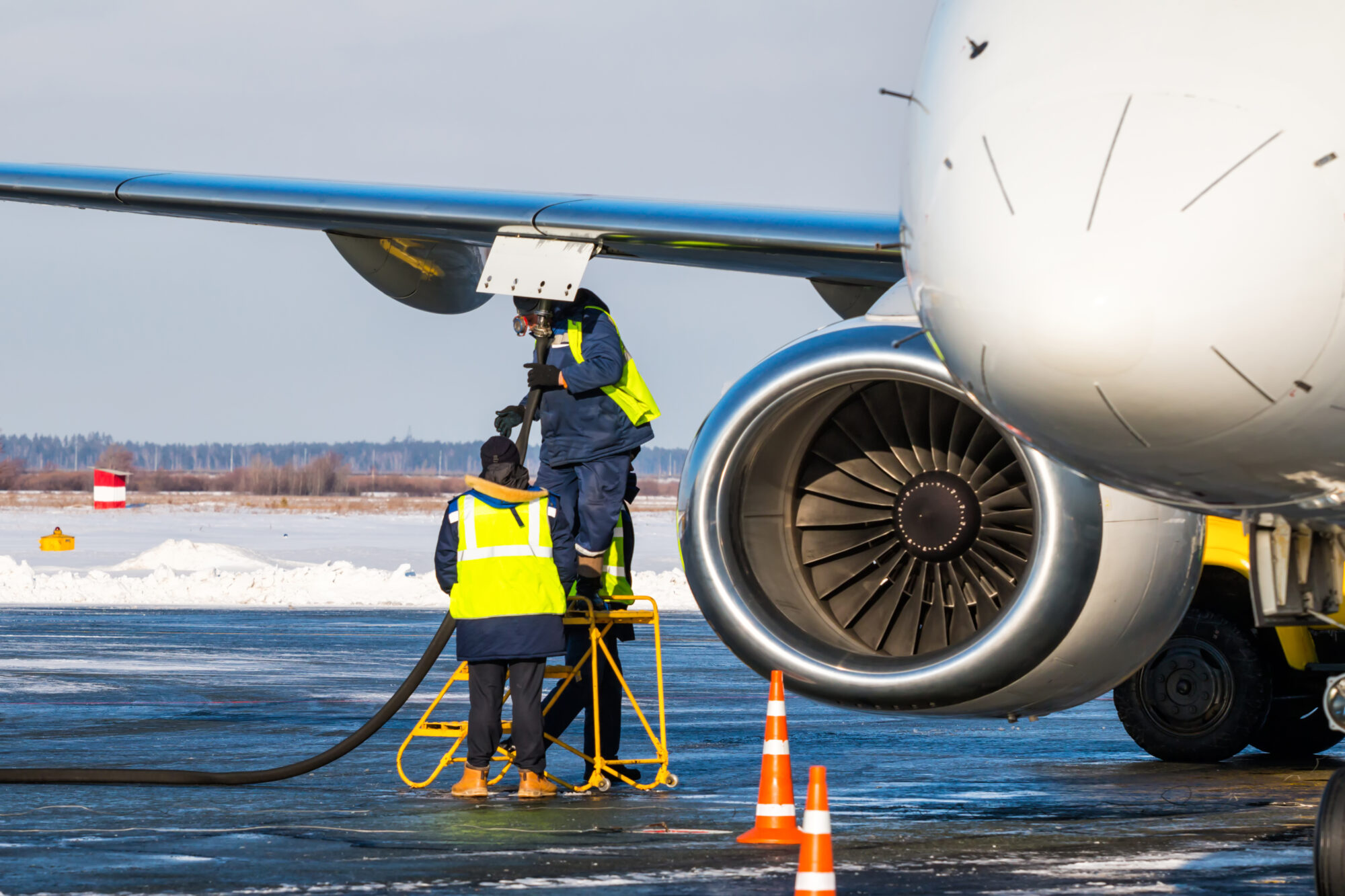
Sustainable Aviation Fuel Innovation Programme
Accelerating the development of UK’s SAF industry and enabling UK Government to achieve 10% SAF in the UK jet fuel mix by 2030. By fostering innovation and collaboration across industry, the SAF IP is building the supply chain, enabling new fuel development and demystifying the SAF landscape.