Unlocking the UK's Circular Battery Economy: Recycling, Repurposing and End-of-Life Strategies
The second Cross-Sector Battery Systems Showcase delivered by Innovate UK Business Connect and the Faraday Battery Challenge, brought together sector experts to share their insights on cross-cutting themes. The session discussed how discarded batteries present new business opportunities for second-life applications and recycling initiatives in the UK.
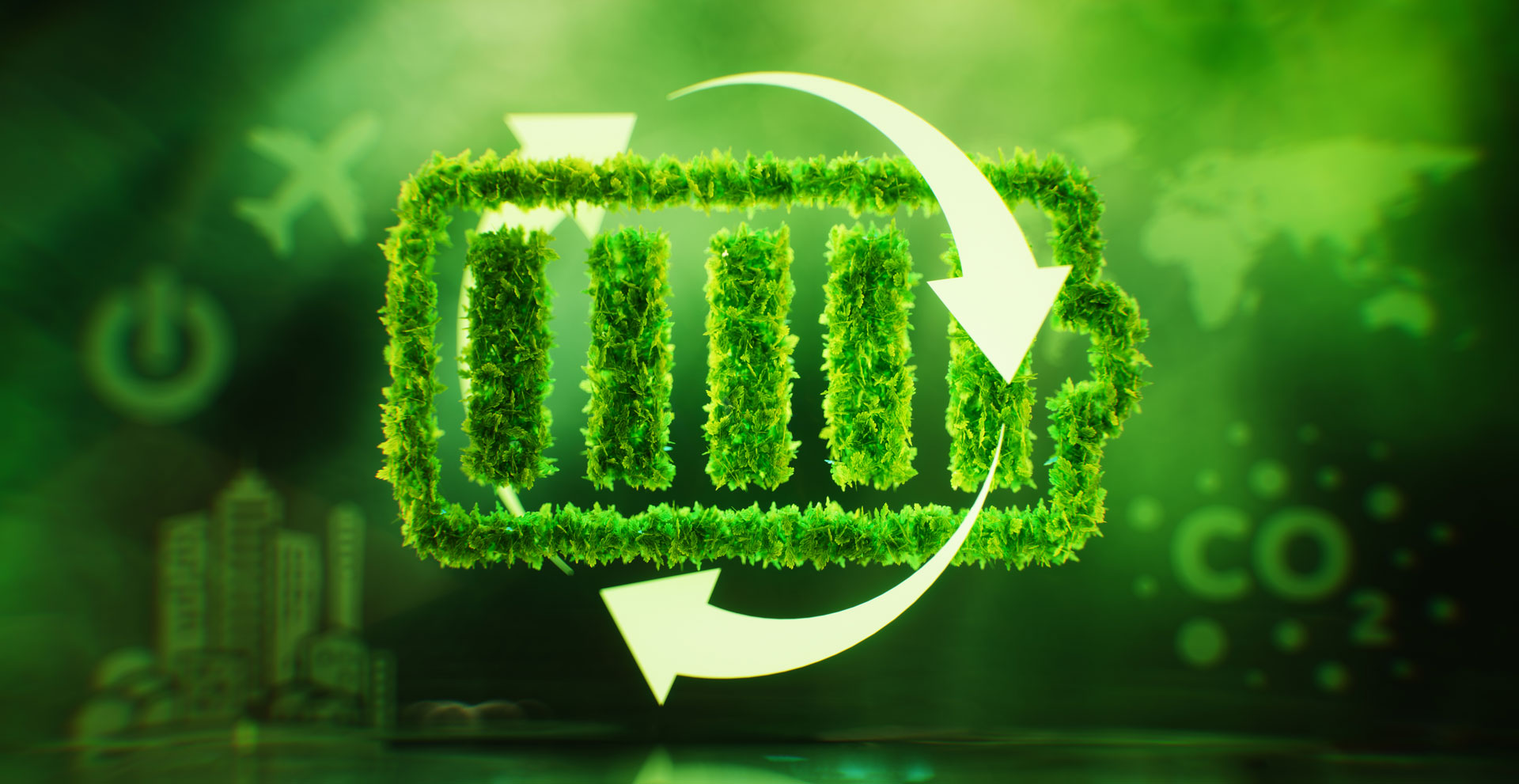
With the rapid uptake of electric vehicles (EVs) crucial for decarbonising transportation and meeting climate goals, it is also important to recognise other industries that are also on their own electrification journeys to net zero. This shift poses challenges in recycling demand and supply chain risks. This session discussed how discarded batteries present new business opportunities for second-life applications and recycling initiatives in the UK.
The panellists for this session included:
- Helen Waters, Head of Electric Vehicle and End of Life Vehicles, EMR Ltd
- Dr. Christian Marston, Co-Founder, Altilium
- Tania Saxby, Head of Sustainability, Connected Energy
- James Corbin, Senior Material Science Engineer, JLR
Repurposing vs Recycling: Two sides of the same challenge
Whilst reuse is desirable, panellists highlighted that it is not always straightforward. OEMs currently prioritise recycling largely due to the uncertainty and risk involved in second-life applications, especially regarding battery safety, liability, and the fact that EV batteries on the road now were not originally designed for second-life use. Some even choose to keep the batteries on their books as assets potentially waiting for positive recycling pricing.
Whilst the technology has been proven to repurpose EV batteries for stationary storage, the challenge lies in convincing OEMs to embrace the circular opportunity and resolve the commercial complexities of asset value, ownership, and liability.
From a business perspective, OEMs face a difficult decision – recycling batteries too early is a cost incurred and writes off their asset value. Panellists highlighted that approaching this through a new ownership model, where OEMs retain ownership through second-life applications, can create new value streams, and still enable eventual recycling to recover critical materials. It was also encouraged by the panel that releasing batteries into the market for recycling or repurposing differs significantly from the traditional procurement process. Instead of focusing solely on short-term cost savings, it is crucial to make decisions that ensure long-term supply chain security.
Repairability and Design
Panellists made the case that design for repair is an underutilised option. While energy storage owners routinely repair systems at cell or module level, this is much harder for EVs due to geographical distribution, required skills, and safety concerns. However, without improved repairability, the industry risks scrapping otherwise usable batteries, moving further away from decarbonisation goals.
The drive for performance has inadvertently created difficulties at the end-of-life stage. Currently, some EV battery packs are highly engineered for energy density, weight, and performance, often making them extremely difficult to repair, disassemble, or recycle.
It is often said that about 80% of a product’s environmental impact is determined in the design phase so early engagement in battery design between cell manufacturers, end-users and recyclers could better facilitate a circular value chain. This early engagement would also allow some level of consistency across disassembly processes, enabling recycling plants to cater to multiple battery types and formats.
Infrastructure Gaps and the Gigafactory Bottleneck
The UK currently has too few recycling facilities including, shredding to black mass and beyond and lacks the local operational commercial-scale hydrometallurgy capacity or cathode active material manufacturing capacity needed to close the loop. Without more UK-based gigafactories and cathode production, even the best recycling efforts may see material exported and re-imported, increasing costs and supply chain risks.
In addition to infrastructure, the security of battery manufacturing and the assurance of knowing there will be sufficient, reliable volumes of battery scrap and a commitment from OEMs to use recycled materials, is essential to making the recycling value chain commercially viable. Without guaranteed feedstock and offtake, the risk of investing in these critical facilities remains high.
Gigafactories, disassembly centres, and refining facilities require capital on the scale of hundreds of millions. The lack of certainty around which supply chain actors will commit first creates a catch-22 situation that is slowing progress.
EMR clearly laid out the investment challenge:
- £2M+ for disassembly centres
- £40M+ for black mass shredding
- £300-600M+ for refining
Each part of the recycling process requires an understanding of volume and chemistry to ensure the processes can be economically viable.
Policy and Regulatory Drivers
Panellists shared how new regulations will soon make end-to-end traceability and circularity a non-negotiable requirement. Companies must invest not just for sustainability but to meet mandatory targets.
The Battery Regulation has set mandated minimum levels of recycled content for batteries by 2031, so at least 6% of lithium, 16% of cobalt, and 6% of nickel must come from recycling, with these percentages rising to 12%, 26%, and 15% respectively by 2036. From 1st February 2027, all EV and industrial batteries over 2 kWh sold into the EU market will require a unique battery passport retrievable using the unique product identifier in the form of a QR code. This means that input and collaboration across the supply chain will be required from mining and refining companies, cell and battery producers, vehicle OEMs, and battery servicing to repair and recycling companies.
Other compliance mechanisms include the end-of-life vehicle directive and producer responsibility requirements which will force OEMs and others to rethink battery lifecycles and secure more sustainable, traceable material supply chains.
Cross-Sector Recycling
EU regulation is driving OEMs to recycling first so that there is enough recycled material to go into the supply chain. Whilst EV battery life is currently around 10-15 years, this means that EVs sold before 2020 and in the 2020s would not be ready for recycling until mid-2030s.
It’s important to recognise there is an unsatisfied UK demand for non-OEM specific cell supply. Other sectors – aerospace, construction, defence, maritime, rail, and stationary storage – also require sustainable battery supply chains. Batteries in aerospace are subject to stringent safety and performance standards, often requiring replacement sooner (e.g., 5–10 years) even if they haven’t degraded significantly.
For the UK’s recycling industry to succeed, early investment in infrastructure must account for these diverse sectors. By developing facilities that service multiple industries, the UK can future proof its recycling ecosystem, ensuring there is capacity to handle the substantial volumes expected in the 2030s and beyond.
Collaboration is Happening – but Needs Scaling
The UK has a strong UK battery ecosystem with players like the Faraday Battery Challenge, Advanced Propulsion Centre, UK Battery Industrialisation Centre and a pipeline of SME innovators.
Some of the key challenges:
- High capex for building chemical refining infrastructure.
- Lack of ownership of battery scrap (urban mining without owning the “mine”).
- Security of stable domestic feedstock from gigafactories.
Despite the challenges, the UK is uniquely positioned. With one of Europe’s highest EV adoption rates, a large second-hand car market, emerging gigafactories, and recycling innovators like Altilium, EMR, and Connected Energy, the ingredients for a closed-loop system already exist. Early collaboration across OEMs, recyclers, and innovators is key.
From 2040 onwards, over 50% of UK battery mineral demand could be met through domestic recycling and the first signs of full circularity have already been demonstrated by Altilium, who have produced the UK’s first EV battery cells using recycled cathode active materials (CAM) at the UK Battery Industrialisation Centre (UKBIC), the UK’s national battery manufacturing scale-up facility.
Handling batteries at the end of life represents a significant opportunity for the UK to manage the battery waste it generates and secure material supply for UK battery production. In order to capitalise on this opportunity, the panellists agreed that this system requires widespread collaboration across the value chain, increased investment to scale technologies and robust regulation to support the production of sustainable materials. Specifically, OEMs. Aerospace and Maritime manufacturers must engage early to design for second life and end-of-life, recyclers need access to stable, local feedstock and offtake agreements and policymakers must create the conditions for investment in recycling and refining infrastructure, including reducing the export of black mass.
Final Thoughts
This is an ongoing challenge which cannot be addressed by a single part of the value chain or through an individual technology, to keep connected to this emerging industry stay part of the conversation by signing up to the Cross Sector Battery Systems Innovation Network.
Related Events and Recordings
Wed
19
Mar
2025
Cross-Sector Battery Showcase - Advancing Innovation Across Industries - 2025
08.30 - 16.30 GMT | Leicester
Watch now
Related programme
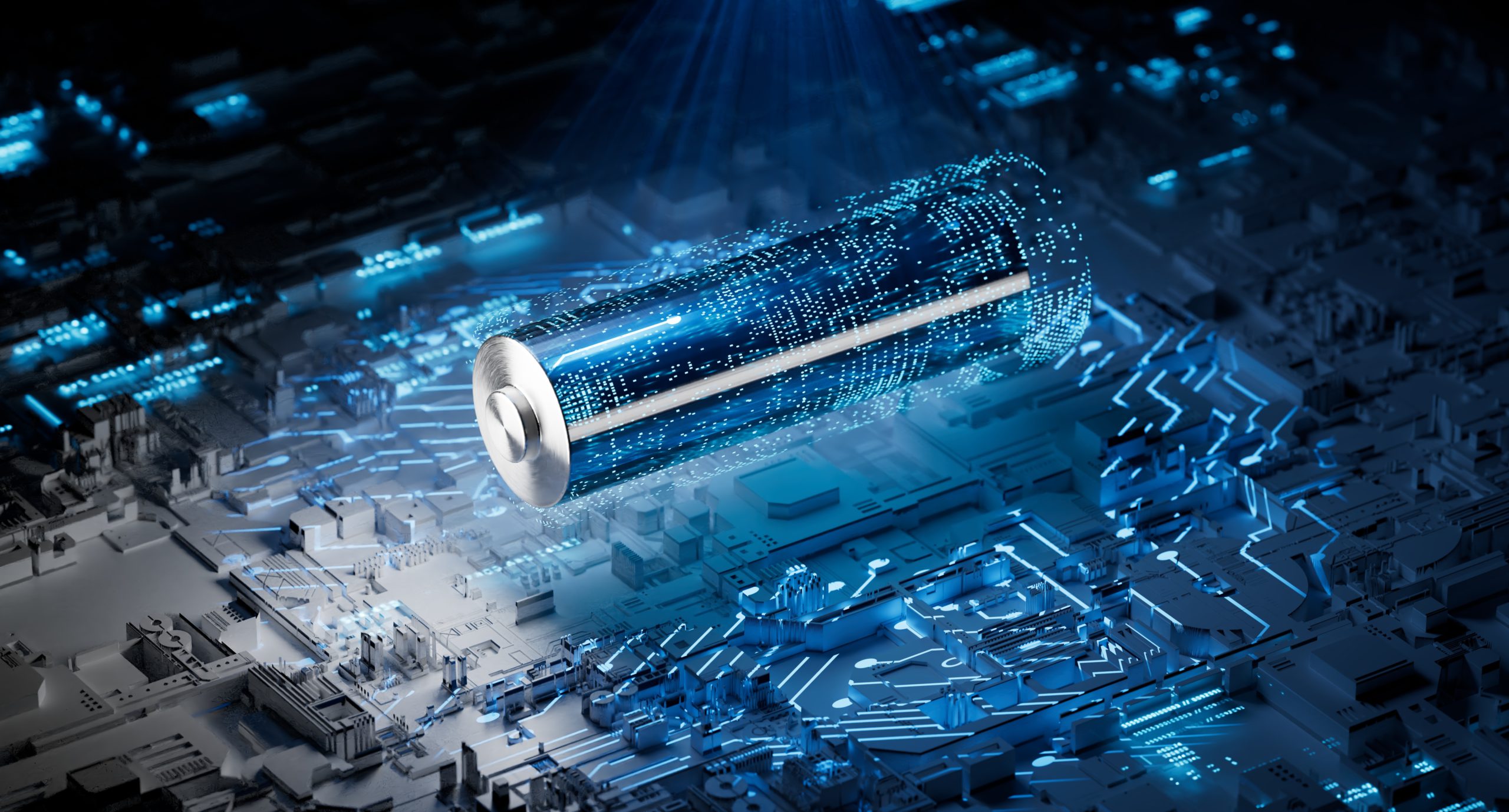
Cross-Sector Battery Systems Innovation Network
The Cross-Sector Battery Systems Innovation Network, co-founded by Innovate UK and the Faraday Battery Challenge, is a cross-sectoral and collaborative community of technology developers and end-users.