Embedding Safety in Battery Innovation
The second Cross-Sector Battery Systems Showcase delivered by Innovate UK Business Connect and the Faraday Battery Challenge, brought together sector experts to share their insights on cross-cutting themes. This session explored the integration of safety in battery deployment across sectors, highlighting challenges in data access, evolving standards, and the interdisciplinary skills needed to build robust, future-ready systems.
As the UK continues its push toward net zero, battery technology plays an increasingly critical role across sectors—from transportation to industrial operations. The second Cross-Sector Battery Systems Showcase delivered by Innovate UK Business Connect and the Faraday Battery Challenge, brought together sector experts to discuss the integration of safety into battery deployment, examining key challenges, driving forces, and the evolving skill sets the industry needs.
The panellists for this session included:
- Jonathan Buston – Principal Scientist, Health and Safety Executive (HSE)
- Simon Williams – Director of Technical Operations and Chief Engineer, Artemis Technologies Ltd
- Tom Maull – Technical Strategy, Elysia – Battery Intelligence from Fortescue
- Julian Fletcher – Technical Development Manager, Great Western Railway
Safety Challenges Across Sectors
Across all sectors, panellists observed that safety standards are still catching up with battery innovation. This lag forces organisations to make risk-based decisions in areas where formal guidance is lacking.
For maritime electrification, the energy demand per passenger is significantly higher than in road transport, presenting major design and integration hurdles. For example, it would be 14 Wh per mile per passenger for a 125 passenger bus, but in marine for a 150 passenger vessel (24 metres, 80 tonnes), it’s approximately 6-700 Wh per mile per passenger. This huge energy demand presents major design and integration hurdles. It was highlighted that marine classification societies are still on a learning curve when it comes to new battery technologies and that low-volume production in marine applications restricts the availability of reliable cell-level data. As a result, managing thermal propagation, a critical issue for offshore and deep-sea, means that early detection systems and proactive monitoring are increasingly favoured over purely reactive safety barriers.
For the rail sector, the risk is managed differently from other sectors. The unique constraints of the rail environment such as fixed trajectories, tight spaces, and high system redundancy, require bespoke solutions. For Great Western Railway’s battery train trials, collaboration with the Rail Safety and Standards Board (RSSB) is key. Whilst standards guide much of the deployment process, they are still evolving to keep pace with the technology, and if there is not a relevant standard, it becomes a question of how you manage that risk yourself.
In high-performance applications like mining and automotive, true performance starts and ends with safety. With programmes deploying millions of cells across a fleet, a one-in-a-million latent defect can have catastrophic effects. Fast charging, wide usable SOC windows, and long life are only possible when you can detect and manage these outliers in real-time. It’s necessary to close the loop between insights and action within the BMS. Whether it’s maximising vehicle uptime in a mine or delivering seamless range in an EV, the ability to safely push performance boundaries depends entirely on knowing your cells inside and out, not just at the beginning of life, but across the battery pack’s entire life cycle.
Low Volume, Low Leverage
As the panel discussion progressed, attention turned to one of the more complex challenges facing all sectors working with batteries: access to reliable, granular cell-level data. Whether it is to qualify a new battery cell, build a safety case, or develop accurate lifecycle predictions, panellists agreed that the data provided by cell manufacturers often falls short of what’s needed, especially in high-safety, low-volume environments like marine and rail.
For maritime applications, while basic performance data (such as internal resistance or cycle life) is relatively easy to obtain, more advanced data required for state-of-health estimation is often out of reach. As the volumes are low marine customers are often left to build their own test programmes or rely on third-party databases, which might not include the exact cells they need to use.
In the rail sector, there is a similarly constrained situation where the battery systems for trains are purchased from a 3rd party supplier and cell-level data might not initially be part of the contract. However, as projects progress, the deliverables could also evolve for example ongoing monitoring and verifying the BMS’s state-of-health reporting with real-world measurements.
Panellists agreed that sharing non-sensitive data that could help improve cross-sector safety mechanisms without compromising competitive advantage and commercial IP.
Managing Change in a Dynamic Supply Chain
From an automotive and mining perspective, there is a different but related issue; cell-level variability. There is an underlying assumption that once a cell is qualified, it’s stable across the programme’s lifetime – but that is not always the case. Driven by ramping production and reducing waste, cell manufacturers constantly optimise their processes; changing coating weights, mixing ratios, or calendaring pressures. Whilst most of these changes are minor, occasionally they can drastically affect cell behaviour, which static data sheets don’t capture. This is where cloud analytics and a digitally connected ecosystem can catch these shifts in real time, where live performance data feeds back into factory processes, enabling proactive adaptation to cell-level variation and supporting more robust prognostic models. This also enables cell manufacturers to ramp their production lines faster, as they are able to correlate production processes to in life performance.
This section of the discussion crystallised a core insight: access to reliable, use-case-specific cell data is a linchpin for safety, though somewhat unevenly distributed across sectors. Whether due to commercial sensitiveness, lack of understanding, or the realities of international supply chains, UK-based integrators are often left to bridge the data gap themselves.
Panellists were clear that progress will require:
- Clearer data expectations and safety use cases from buyers and regulators
- Stronger cross-sector collaboration on non-competitive datasets
- More digital infrastructure to track and analyse cell performance across the asset lifecycle
The Skills Behind Safe Systems
The final part of the discussion honed in on the skills and capabilities needed to support efforts in safety integration. It was noted that many industries still operate in disciplinary silos but battery system developers need these teams to fuse together.
Across the panel, four critical skill areas emerged:
- Electrochemists – understand battery nuances at the electrode level and make informed decisions on state-of-health.
- Data scientists – can extract meaningful insights from performance data, how best to use the assets etc.
- Electromechanical engineers – from busbar fatigue to thermal equilibrium, they are critical to creating robust and reliable designs.
- Systems engineers – can integrate thermal, electrical, mechanical, and software domains into coherent safety frameworks.
Often, the right expert already exists, but not in your sector. As we aim to build safe, efficient and long-lasting battery systems, the ability to collaborate across traditional disciplinary lines may be just as important as the technical standards we apply.
Final Thoughts
Innovation in battery technology is outpacing the frameworks designed to govern it. As use cases expand and safety demands intensify, collaboration across sectors, disciplines and geographies is essential. To keep connected to relevant initiatives, stay part of the conversation by signing up to the Cross Sector Battery Systems Innovation Network.
Related Events and Recordings
Wed
19
Mar
2025
Cross-Sector Battery Showcase - Advancing Innovation Across Industries - 2025
08.30 - 16.30 GMT | Leicester
Watch now
Related programme
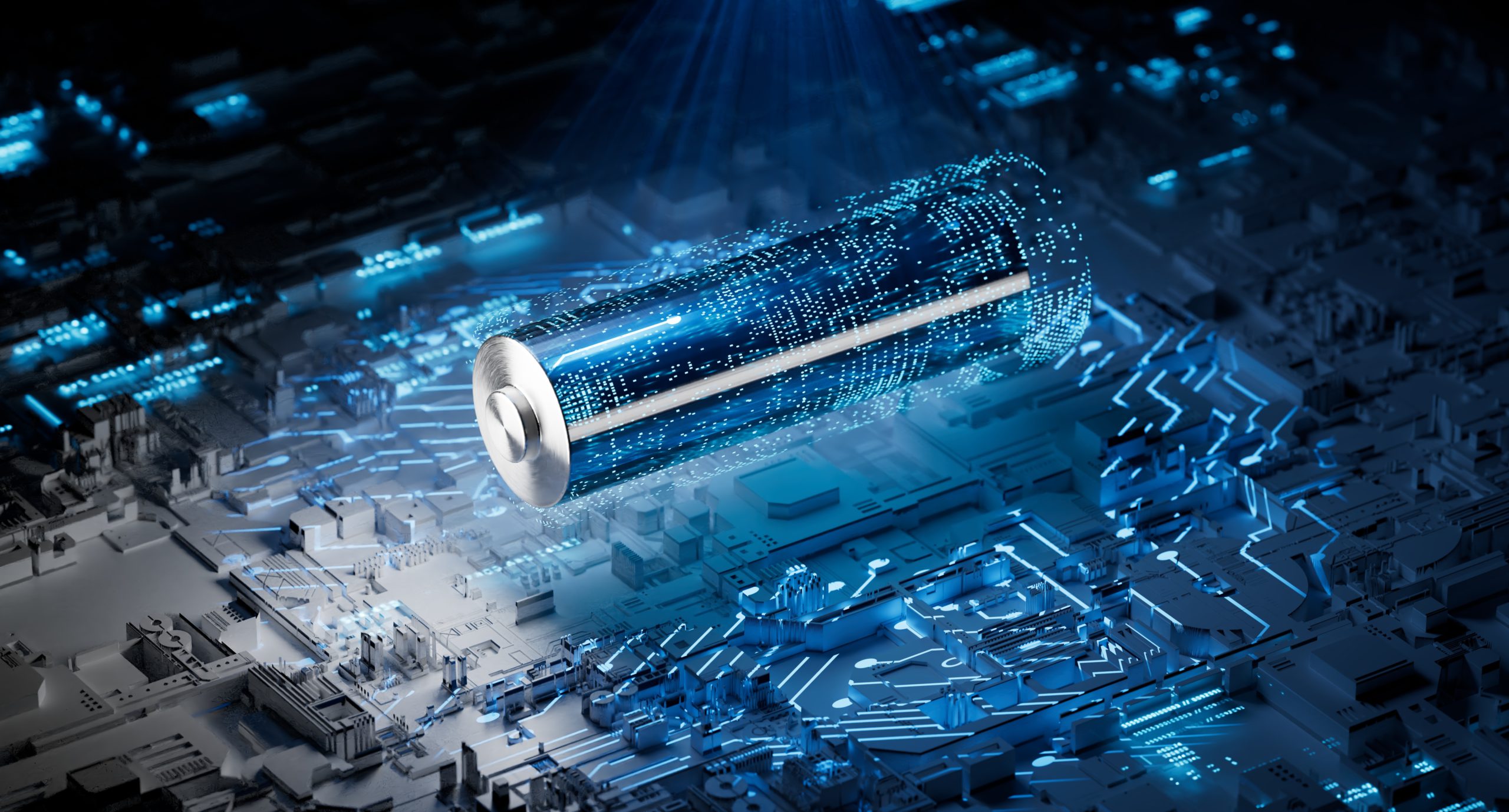
Cross-Sector Battery Systems Innovation Network
The Cross-Sector Battery Systems Innovation Network, co-founded by Innovate UK and the Faraday Battery Challenge, is a cross-sectoral and collaborative community of technology developers and end-users.