Cross-Sector Battery Transition: Supply Chain Strategies
The second Cross-Sector Battery Systems Showcase delivered by Innovate UK Business Connect and the Faraday Battery Challenge, brought together sector experts to share their insights on cross-cutting themes. This session explored the evolving battery supply chain needs of non-automotive sectors, highlighting the challenges of low-volume demand and the collaborative strategies required to ensure safety, sustainability, and system-wide resilience.
As the global shift toward electrification accelerates, non-automotive sectors, such as aerospace, defence, maritime and rail, are navigating distinct challenges in securing resilient, high-performance battery supply chains. With smaller volumes, longer asset lifecycles, and demanding regulatory and safety requirements, these industries must take a strategic and collaborative approach to sourcing, qualification, and long-term supplier engagement. The second Cross-Sector Battery Systems Showcase delivered by Innovate UK Business Connect and the Faraday Battery Challenge, brought together industry experts to share a cross-sectional view of how battery technologies are being adapted and to delve deeper into the complex topic of supply chains.
The panellists for this session included:
- Richard Wilding OBE – Self-Employed, Emeritus Professor of Supply Chain Strategy
- Kate Cooke – Energy Sources Senior Manager – Propulsion Electrification, Collins Aerospace
- Alexander Wallace – Senior Scientist, Defence, Science & Technology Laboratory (Dstl)
- David Wing – Project Director, Houlder
- James Wright – Product Manager, Decarbonisation, Angel Trains
Automotive as a technology driver – but not always a template
The automotive sector is currently the largest consumer and innovator of battery technologies. The panel explored how much of an influence automotive has on their respective sectors (aerospace, defence, maritime and rail). The panel’s consensus was that while automotive drives progress across these industries, not all sectors can follow directly.
For rail and maritime, these sectors are often technology adopters rather than developers, and so the influence is more about systems integration than chemistry, with the innovation lying in areas such as packaging, containment, and cooling systems.
In contrast, aerospace is intentionally pulling insights from both traditional automotive and high-performance motorsport. But the sector is moving beyond simply adopting automotive technology and instead redefining battery safety, system design and circularity with aerospace-grade expectations, given aircraft can be in service for 30 years.
It was highlighted that there is a growing divergence in defence needs and there are considerations if a dedicated defence supply chain may be necessary. For example, the use of 18650s when automotive favoured them but as automotive is shifting to larger cell formats like 4680s, these are impractical for certain defence applications.
Supply Chain Engagement
With all panellists representing sectors where demand for batteries for electrified products is modest compared to automotive, the conversation turned to how to maintain supply chain interest. Of the predicted UK demand of 115 GWh/yr in 2035, aerospace, defence, maritime and rail together make up less than 3% of this total, making it very difficult to influence the battery market alone.
From the defence side, longevity and niche applications make standardisation difficult. Some systems stay in service for 40 years and defence requires energy-dense chemistries, but when cost reduction becomes the focus for automotive, like with LFP chemistries, it can be a challenge to meet defence needs. In a time where supply chain resilience and transparency are critical, the UK defence market can collaborate with NATO and Five Eyes countries to coordinate demand, creating a viable commercial market for cell suppliers.
For aerospace, similar asset lifecycles of up to 30 years mean that consistency and reliability across their supply chains over decades are critical. Aerospace must maintain strict control over battery cell characteristics to avoid disruptions to system performance and certification. To manage this, aerospace organisations are actively building strong, strategic relationships with select suppliers, particularly those focused on energy dense cells, and integrating risk monitoring into their entire propulsion system design. While the cell itself is a key component, leveraging broader organisational capabilities such as existing production infrastructure for motors and electronics and batteries for secondary systems can help to reinforce their position.
For rail, there is a major coordination challenge due to its highly fragmented structure, involving numerous operators, infrastructure managers, and regulatory bodies. Successful deployment of battery-powered trains relies not only on the technology itself but on systemic alignment, ensuring everyone understands the operational constraints and infrastructure requirements. Maintaining effective supply chain engagement in this environment means developing common standards, clearly defining system interfaces, and ensuring all stakeholders from OEMs to operators are aligned on expectations. It’s less about negotiating high-volume supply and more about creating interoperable, resilient systems where battery performance, safety data, and digital communication flow seamlessly across a complex network.
In maritime, the core supply chain challenge lies in regulatory complexity and the lack of deep in-house battery expertise among regulators. Marine operators, especially smaller ones, often face significant risks when adopting battery technologies due to unpredictable hazard assessment outcomes. These assessments depend heavily on supplier data and expertise, as regulators cannot realistically maintain chemistry-specific knowledge at scale. For ship owners working with tight margins such as high-speed hybrid vessels, any unexpected changes in weight, size, or power draw can have significant operational and commercial consequences. Therefore engaging with the supply chain is not just about securing reliable components but also about navigating a regulatory grey area where clarity is lacking. An ideal future would strike a better balance between flexible, risk-based approaches and clearer, more prescriptive standards—giving operators and suppliers more confidence to invest, design, and deliver without fear of regulatory surprises.
All of these low-volume sectors must articulate long-term value and reliability to keep supply chain buy in as they scale operations.
Emerging Chemistries
Emerging chemistries were discussed largely in the context of safety, recyclability and long-term sustainability. Battery chemistry is not just a technical choice but a long-term strategic bet, with ramifications stretching across asset life cycles, integration costs, and global supply dependencies. The current state of geopolitics causing mineral bottlenecks is amplifying these concerns.
Aerospace and defence sectors are particularly focused on how new chemistries like solid-state or advanced NMC variants might address performance without compromising on reliability or regulatory compliance. Both sectors have long development cycles and rely on stable, strategically managed supply chains. Unannounced changes such as cost-cutting measures or automation in production that could alter a cell’s characterisation can have serious implications, potentially affecting how the cell behaves within the wider system or module.
For maritime, the risks are playing out in real-time. Ten years into operating the UK’s first hybrid ferry, Houlder are now facing a decision that’s as technical as it is regulatory; whether to replace the cells or the whole battery system. The maritime sector is slowly adapting from a prescriptive approach to risk-based approval which requires a different skillset to adequately manage. Regulators need to improve their risk evaluation capabilities, and operators need to enhance their ability to identify, communicate, and manage risks effectively. Flexible, risk-based approaches would give operators and suppliers more confidence to invest, design, and deliver without fear of regulatory surprises.
Battery Passports
By 2027, every EV and industrial battery in the EU will require a Battery Passport—a digital record of what’s inside, where it came from, and how it’s been used. For most sectors, this is a welcome evolution. Collins Aerospace see this as an area for early engagement, as it’s vital for traceability, emergency response, and ultimately, circularity. They are already designing battery systems with end-of-life disassembly and material recovery in mind, ensuring high energy density batteries can be used for second-life applications across ground services, and ultimately aiding recyclers at the end of service life.
Other sectors flagged blind spots, for maritime, once the battery is in service, who maintains it – the supplier, the operator, or the asset owner?
For rail, whilst the onus lies on the OEMs rather than asset owners, it opens a path to better reuse with the passports providing a foundation for second life strategies as well as emergency response to battery faults. Knowing how a battery lives helps decide how it should retire.
Under the EU’s Battery Regulation, batteries used for national security and defence purposes are exempt from the requirements of a digital battery passport. This exemption also applies to equipment directly related to the protection of Member States’ essential security interests. However, whilst these exemptions provide important flexibility, the defence sector cannot afford to overlook the wider implications for the battery supply chain. With such a small share of global battery demand, defence relies heavily on civilian market developments and shifts in regulatory requirements will inevitably cascade through the supply base. As such, maintaining engagement with sustainability standards and commitments, traceability protocols, and circularity initiatives remains crucial.
Final Thoughts
From the stories shared across our panel, leaders in aerospace, defence, maritime and rail talked through a common pattern: we are not just building systems with batteries, we are building systems around them. The challenge now lies in maintaining momentum and developing supply chains that are agile, collaborative, and tailored for diverse use cases. To keep connected with UK battery stakeholders and supply chain players, stay part of the conversation by signing up to the Cross Sector Battery Systems Innovation Network.
Related programme
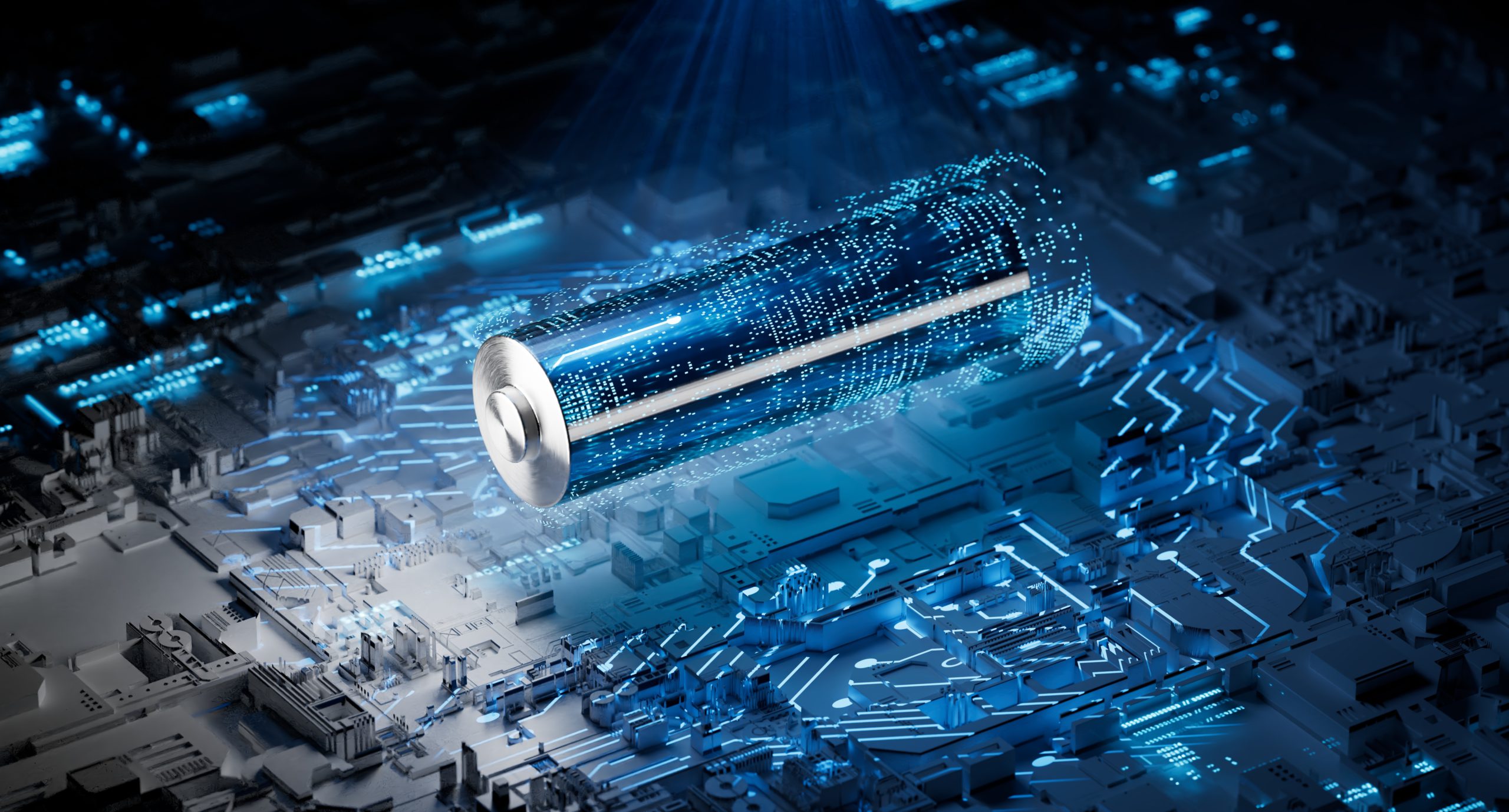
Cross-Sector Battery Systems Innovation Network
The Cross-Sector Battery Systems Innovation Network, co-founded by Innovate UK and the Faraday Battery Challenge, is a cross-sectoral and collaborative community of technology developers and end-users.